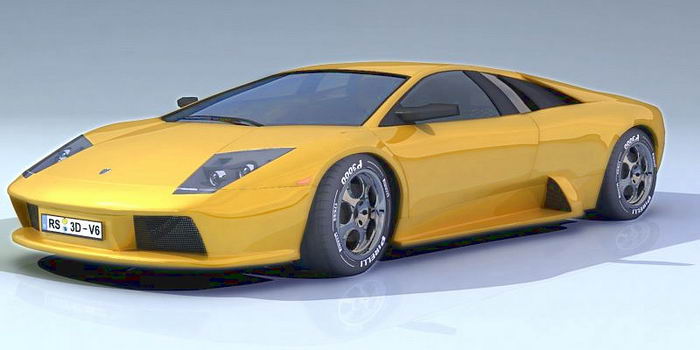
Creating a Lamborghini Murcielago
This multi chapter tutorial shows in detail how to create and render a very special car, the Lamborghini Murcielago, in Realsoft3D V5. The tutorial will go through all the steps and contains over 350 pictures showing the workflow.
Some basic knowledge of using the Realsoft3D user interface, like creating and renaming objects, using the compass menu and changing views is required. If you are unfamiliar with this, please check the user manual. This tutorial covers both SDS modeling and NURBS modeling. As you will see, the basic modeling techniques we used are the same all the way. So, some parts of the tutorial show more images then text. Where things become tricky, we explain the steps more in detail.
We hope you have as much fun trying this tutorial (oh… and maybe learn a thing or two), as we had creating this!
The Lamborghini Murcielago we are aiming for here…
Robert den Broeder and Stefan Klein, July 2006.
Special thanks to Vesa Meskanen for his excellent car paint shaders! Extra special thanks to Arjo Rozendaal and Boris Jahn for proof reading and testing our little tutorial
Last update: July 27th 2006
Intermediate/advanced level.
Reference images
If you wish to accurately model a car like this, you need so called reference images. These images help you creating the car using the correct proportions and dimensions. You can use blueprints and real photos for that. There are many websites that have such images. For this tutorial we used this image. It shows the car from four different views and we are going to use these different views in the modeling process. We have cut up the image and saved each view as a separate image with names like ‘top‘, ‘side‘, and so on. Click on the image for a ZIP file containing the four separate reference images cut out for you.
The Lamborghini Murcielago reference image. It shows all dimensions measured in millimeters.
Each image will be mapped on a separate rectangle later on, each representing a different view.
Setting up the modeling environment
Start Realsoft3D. The first thing to do is to set the metrics for the modeling environment to proper values. Select the File -> Preferences menu. The Options window shows. Click the Metrics tab and set ‘Distance‘ to cm (centimeters) and make sure the ‘Three fields‘ option is checked.
Distance in centimeters and Three fields option checked.
This next step is optional. Many people like to use the Quadview environment when modeling cars. If you do not have this as default working environment, you can select it using the Environments -> Quadview menu option. This divides the modeling part of your screen in four parts. Each part can use its own view on your project (front, side, top and perspective). You can use the camera icons on the right-hand side of the screen to change the views for each window. You can switch between wire frame and OGL display independently for each window. You can even render each window separately if you like. If you wish to enlarge a particular view, simply double click it. To return to normal size, double click it again. Make sure you use parallel projection for the front, side and top view (you see no ground plane in the view window). Also hide the grid and disable snap-to-grid.
Now in the Select window, directly under the Root level, create a new level (press Shift + L) and rename this level to ‘Blueprint‘. With the new level selected, press the Tab key, to make it the current level. You can tell it’s the current level, because there is a black dot shown left of the level icon. Now all new objects will automatically be created in the current level. If you wish to change the current level back to Root, select the Root level and press the Tab key again.
Take a top view and create an Analytic rectangle. Make the rectangle more high then wide. Move the rectangle so you can see the world XYZ axis at it’s centre. Note that when you work in Quadview mode, you see this rectangle also in the other views. Rename the rectangle to ‘topview‘.
Blueprint level contains a rectangle called ‘topview’
Select the ‘topview‘ rectangle and open the properties (press ‘p’ key). In the Property window, click the Spec tab. We will model the car in a scale of 1:1. To get to a proper 1:1 scale, we must use the dimensions of the blueprints we use (and not the dimensions the car has in reality). So, use your favorite paint program or file manager and check the dimensions (length and width) of the blueprint images you use. In our case: 545 by 267 pixels. See next screenshot:
Paintshop Pro 8 screenshot, showing the dimensions of a blueprint image
In the Lengths section, set the Width of the rectangle to 267 (cm) and the Height to 545 (cm).
If, after changing the properties, the rectangle gets too big to be displayed, simply drag&drop the topview object from the Select window on your view window and the viewcam position will change so the entire object can be displayed.
Spec tab defines dimensions of the rectangle. Col tab defines and positions the texture.
Go to the Col tab and use the Texture field to select the reference image representing the top view of the car. Also, set the Rotate values as shown in the screenshot above. In the Surface properties section select the Illumination attribute from the drop down list. Set Illumination to 1,00 1,00 1,00 (pure white if you use the RGB color scale). See next screenshot:
Illumination set to white
Click the Wire tab and set Texture quality to ‘512’ or better. It may also be a good idea to set Forced visibility to 0,5. The forced visibility parameter helps you to see the lines of the blueprint while modeling the car parts. Compare the next two screenshots to see the difference:
Forced Visibility 0 (zero) Forced Visibility 0,5
Take a front view and repeat the previous steps to create the frontview rectangle. Use the following dimensions for the frontview rectangle: width 267cm – height 132 cm. When done, take a side view and create the sideview rectangle. Use the following dimensions: width 545 cm – height 132 cm. Also, rotate the texture like shown in the next image:
Rotate values for the sideview rectangle
The rear view rectangle will be added later.
Now these three rectangles need to be carefully positioned, like shown in the next screenshot. It’s a good idea to switch to wire display mode first, to make sure the rectangles are properly aligned and not sticking out somewhere. When the images are not properly aligned you will run into troubles while modeling:
All three rectangles in place (perspective projection, OGL display mode).
When done, save your project. It is a good idea to use different project names every time you save a newer version (e.g. Lamborghini001, Lamborghini002 etcetera). This allows you to go back to an older version if you desire to do so.
Modeling the hood
It’s time to start modeling the car now and we start with the hood. During the modeling process we only build the right half of the car, the left part will be created using an instance. These two parts will be welded together in the end.
Make sure you are in OGL (shaded) display. Take a top view, and zoom in so you can clearly see the outlines of the car. Create an SDS rectangle, use 4 vertices in the U direction and 4 vertices in the V direction and use the ‘Smoothen to nurbs‘ type, like shown in the next screenshot:
The options are set for the SDS rectangle
Draw the rectangle and position it right off centre on the hood, when seen from the top (see next screenshot). While drawing the rectangle you will see that the appearing object seems to be smaller then what you actually draw. Don’t worry about that, it will be corrected later on. While drawing the rectangle, you might find it appears under the textured rectangle. If this happens, simply move the textured rectangle down a bit, or move the SDS rectangle up until it appears. When done, rename the rectangle (called subdiv2 or so) to ‘Hood’.
SDS Rectangle in position
It may be easier to work with an object that has a contrasting color, compared to the background. To achieve this, select the Hood in the hierarchy, open the Property window (press ‘p’ key) at the Col tab and select for instance a bright yellow color. Your hierarchy now looks like this:
The Hood added.
With the Property window still open, click the Spec tab. In the Rendering section, set the ‘Interpolate Boundary‘ option. Note, that when you set this option the rectangle grows bigger. Go in Point Edit mode and select the all the left side points of the Hood. Check at the Spec tab that the X-coordinates of these selected points are 0,00 (Selected Points section, the left most position should be set to 0,00). This is important later on when we create the whole car out of a modeled part and an instanced part. You may also need to reposition the Blueprint level to align it again with the Hood. Do not move the Hood, because you then will change the X-coordinate of the object again.
X-coordinate of selected points set to 0,00
Click the Wire tab and set the ‘No shading‘ option (this hides the solid look of the mesh) and uncheck the ‘Hide Coordinates Handle in Edit Mode‘ option and close the Property window.
Click on the Hood object in the Select window and make sure you are in Point Edit mode (use the compass menu, or the Edit drop down menu to switch edit modes). The Hood is displayed as a grid with red dots. The red dots are points in the SDS rectangle you can move around to change the shape. Note that when you click such a dot, it changes to a yellow color. Also you see a coordinate handle appear. You can use these to move points around.
Point edit mode selected
Now simply drag and move the points to match the right side outline of the hood. It will take some time and effort to get the points just in the right position. It is very important that you keep the lines between dots as smooth as possible. This will give you the nicest renders in the end. After some point editing you get something like this:
The right side of the hood modeled in top view
Now comes the tricky part: to make the points also match the outlines when seen from the other views! This is the point when you have to be sure that the reference images are properly aligned! First take a side view and move complete rows of points, to make them match the outline. This take just a little practice. Then move to a front view and repeat the matching process. As said before, try to keep the hood as smooth as possible, to prevent render errors later on.
The hood seen from different angles, matching the outlines. Top right is a test render.
When done, we are ready for the next step: editing the edges of the Hood. So, take a top view and switch to Edge Edit mode:
Edge edit mode selected
We need to select all outer edges, except the left side. An easy way to do this is to click the right side middle edge and click the Loop tool icon (see next screenshot). Then click the Loop tool icon four times, and so add the required edges to your selection. Then open the Property window, click the Spec tab and in the Selected Edges section, set the Edge Sharpness to ‘Free‘.
The first edge selected and 4 clicks later… ..all edges selected, except the left side.
Take a front view and hover the mouse pointer over a selected edge. Note that the shape of the pointer changes into a small pointed cross. Press and hold the Ctrl button and drag the selected edges down a bit. This creates a small beveled side on the hood, giving it some depth.
A test render now shows corners that are too round. In the corners we need sharp edges. Select all edges around the corners (as shown in the screenshot) and for these edges, set Edge Sharpness to ‘Free‘ as well. If you now render the Hood, you see sharp corners.
note: The instructions you read for edge sharpness are suggestions. The tutorial is meant to be a guideline, not a rule book . If you prefer to use free edges instead of sharp, or semi sharp, then by all means go ahead! During proof reading of this tutorial, people showed they have developed their own preferences with regard to SDS modeling. This, of course is a good thing and we don’t want to change that. Just try and see what you think is best for your model.
These corners are too round… Select these edges (including the vertical ones!)
Much better now! Sharp corners!
As said before in the beginning of this tutorial, we will make use of instances to model the other half of the car. To let an instance create the other half of the Hood, we need to make some adjustments in the hierarchy first. Create a new level (press Shift + L key) and rename the new level to ‘Lamborghini‘. Drag and drop the Hood object in the Lamborghini level. To create the instance of the Lamborghini level, press and hold the Alt key, and then drag and drop the Lamborghini level on the Root. This creates a new object in the hierarchy, called: instance0(Lamborghini). Your hierarchy now looks like this:
Instance created!
The new instance object is in exactly the same position as the original. They overlap and thus you see only half of the Hood. Now we will move the instance into position using the Mirror tool. Take a top view, select the instance in the hierarchy, click the Transformation tab and then the Mirror tool. Draw a small box at the top left corner of the original object. The instance object immediately mirrors. To finish the operation, draw a second box at the bottom left corner of the original object. This snaps the mirrored object in position. Make a test render to check your results. Maybe you also wish to do some more point editing to enhance the shape of the hood. You could decide add some extra lights to the scene and drop them into a separate level (Lights) in the hierarchy. When ready, it is a good time to save your work.
The Hood is complete and consists of an original and an instanced object
The fun part is that every modification to the Lamborghini level, will immediately be done to the Instance as well. Try this: create an analytic cube anywhere in the view window. Next drop the cube in the Lamborghini level and notice that a mirrored version of the cube is created immediately! Now delete the cube.. it’s not part of this tutorial ;-)
Creating the Mudguard
To create the Mudguard, start with making a copy (in the Select window, click right mouse button and select Duplicate from the pop-up menu) of the Hood and then rename it to ‘Mudguard‘. While working on the Mudguard, it is easier to set the Hood object to Wire Frame invisible (WF-Inv). This helps to keep the view clear of objects you don’t need or do not want to see. You can find the necessary controls for this in the MiscTools toolbar, which is located right below the Select Window. If the toolbar is still hidden, simply click on the blue MiscTools bar to open it.
Select an object and click the WF-Inv icon
Go to Face Edit mode and select all faces, except the ones on the vertical side. Then use the Destroy Faces tool (Note: do not use the ‘Destroy Faces, keep orphan vertices’ option!) to delete the selected faces. The vertical edge remains. Move the remaining part just a little to the right, to create a small space (this is the seam between the two car parts) between the Hood and the Mudguard.
Some tips regarding selection and de-selection of points, edges and faces. There are some very nifty keyboard shortcuts that make the life of a modeler a little easier. They work the same for all editing modes (point, edge, face). We list a few here:
* Select all : Ctrl + a
* Deselect all: Ctrl + t
* Invert selection: Ctrl + i
* Press and hold the Shift key to add something to your selection.
* Press and hold the Alt key to remove something from your selection.
Select these faces and use Destroy Faces.. and you end up with this after destroying selected faces..
Now go in Edge Edit mode and select the upper edges of the remaining faces. Hover the mouse pointer over a selected edge, so it changes shape (pointed cross). Press and hold the Ctrl key and drag the mouse to the right. This creates new faces, which will form the top of the Mudguard.
Note: if you use the blue face handles for this operation, you will not get the correct results.
Select these edges.. Press and hold the Ctrl key and drag to add new faces
After the first extrude, you can delete the original vertical faces from this object, they are no longer needed.Now with this simple technique its just a matter of adding faces and moving points around, and thus keep the shape matching the blueprint pictures. Sometimes check your progress with a test render. While modeling, keep an eye on the important contours of the car model. Note (see next image) how the mesh and the red lines match the headlight area and this grey line along the side of the nose. This is important, because later on we need to work on these areas.
Mesh matches headline area (top view).. New faces added..
Edges selected, ready to be split!
To get the wheel area smooth we need to split the edges into smaller pieces. This gives more control over the points in this area. While in top view, select the edges on the right side of the Mudguard (see above image on right side) and use the Split tool (default value of 1 split will do).
Split tool Split tool options
After performing the split, switch to Point Edit mode and drag the points into position around the wheel area
Points in the wheel area moved into position.
Now again it’s a matter of moving the points around. One area requires special attention. Switch back to Edge Edit mode and select the edge as shown in the next image:
Select this edge and Ctrl+drag down to create new faces All faces created and points in place
Switch to Point Edit mode and move the points into place. Of course you have to check all three views to see if the points are correctly positioned.
Now for some final touches. First switch to Edge Edit mode and select all inner edges of the wheel area. Press and hold the Ctrl key and move the mouse down just a little, to create new faces again. Switch back to Point Edit mode to make necessary adjustments.
Edges selected… New faces added (shown in edit face mode)
The next step is to make some edges sharp, so the model will match the reference image. The lines are marked red, for your convenience:
These red lines indicate where the sharp corners must be in your model.
Switch to Edge Edit mode. Select the edges that represent the lines marked red in the image above. Edges sharpness is controlled in the Property window at the Spec tab. Select the Mudguard object in the hierarchy and open the Property window at the Spec tab. In the Selected Edges section, select ‘Sharp’ from the drop-down list. This makes all selected edges sharp.
Selected edges are set to Sharp, thus creating sharp corners
When done it is a good time to save your project. Here is a test render, showing what we have accomplished so far:
Test render showing the sharp edges
Headlights
The next step is to model the headlights. Before we start modeling, we make a copy of the Mudguard object and make it Wireframe invisible. This copied object will later be used for modeling the glass of the headlight.
First we model the Casing for the headlights. Select the Mudguard object. Take a top view and make sure you are in Face Edit mode. Select all faces in the headlights area as shown in the next image:
All faces of the headlights area selected
Take a side view and use the Extrude tool to move the selected faces down, just a little at first. This creates nice sharp edges for the casing. Then extrude again to complete the shape of the Headlight Casing (simply use the ‘Again‘ option from the right mouse button pop-up menu!). When the shape of the Casing is ready, rotate the bottom faces a little to realign them with the blueprint image.
Press the right mouse button in the view window to get this
pop-up menu
Note that your current object still is the Mudguard object! To make the Headlight Casing a separate object (which makes the texturing process easier later on), simply duplicate the current object. Select all faces that are not a part of the headlight casing and delete them, so only the Headlight Casing is left. Rename the current object to ‘Headlight Casing‘.
Now the Mudguard object also contains the headlight Casing faces. These are no longer needed, because we made the headlight casing a separate object. So, select the Mudguard object, select all faces, except the first row, that form the shape of the Headlight Casing and delete them. The result is a Mudguard object with space for the Headlight.
Now select the first copy of the Mudguard that we made Wireframe Invisible and make it visible again. Select all faces, except the Headlight area and delete them.
All faces of the Mudguard selected, except the Headlight area. Delete them!
The result is a set of faces that form the shape of the glass of the headlights. Rename this object to ‘Headlight Glass‘. Note that you only made copies of the Mudguard object and that none of these copied objects have moved! Your hierarchy now looks similar to this:
The hierarchy after creating the headlights
Almost done now. The last step is to add a vertical edge to the Mudguard object, similar to what we did with the Hood object. So, select Edge Edit mode, select the Mudguard object, then select all outer edges of the Mudguard. Press and hold the Ctrl button and move the mouse down a little, just like you did before.
Extra vertical edge added to the Mudguard object.
And of course, save your work before continuing. Here is a test render of the car so far. For clarity, all objects have a different color.
Test render showing all different parts in different colors.
Front spoiler
The next part of the car we will model is the Front spoiler. This is a very complex object and will take some time to create. First duplicate the Hood. Then make the original Hood WF-invisible. Make sure you are in Face Edit mode. Select the object called ‘Copy of Hood‘ and rename that to ‘Front spoiler‘. Now, select all faces of the Front spoiler, except these at the front rim, like shown in the next image:
All faces of the duplicated Hood object deleted, except these at the front rim
Take a top view and go to Edge Edit mode and select the upper edges to create new faces, just like you did before. Creating new faces from the upper edges makes sure the spoiler also has a vertical edge, which you need. Keep creating new faces, switch views when needed and use point editing to match the blueprint.
The red arrow indicates how the shape of the spoiler should develop
new faces match the blue print (side view)
When the Front spoiler has the shape like shown in the last image, take a front view. We need to add some extra edges to the object. The Front spoiler contains large air holes, which we need to cut out from the spoiler. Because we use an instance object, we only need to model one. Modeling this is easy if you have edges at the same position as the air hole has in the blueprint. So, when in front view, go to Face Edit mode and use the Knife tool to cut some new edges to match the blueprint. Be aware that there are two knife tools available! You need the one in the tool control bar, which is shown in the next small image:
The knife tool you need… Edges added, to match the blueprint
The next part is a little bit tricky. The cuts you made basically divides the object in faces that will be used for modeling the air hole; the others will be used for the front spoiler. Next images show how to proceed. The edges which are marked red, are extruded downwards, just like you always did. The blue edges you need to extrude inward. They shape the inside part of the air hole. When modeling the air hole you will notice that you need to weld two open ends together. Don’t worry about that, we will fix that later on.
Edges marked red are extruded down, the blue edges are extruded inwards
Now continue modeling the mesh in Edge Edit mode and finish the shape of the front spoiler. The areas around the Head light and the Mudguard are first roughly modeled. We will fine tune the shape later in Point Edit mode.
In edge edit mode continue modeling along the lines of the blueprint
The front spoiler almost done now!
When the Front spoiler has the shape, similar to this image shown above, it is time to do some fine tuning. The fine tuning process is best performed in Point Edit mode. Let’s start with the point where the wheel area (Mudguard) and the Front spoiler come together. The points of both objects (Mudguard and Front spoiler) need to be in the same position. Later we will move the points of the Front spoiler a little down, to create a seam.
To accomplish this, we have a neat trick up on our sleeves. Perform the following steps (read carefully!). Set both the Front spoiler object and the Mudguard object in Point Edit mode. Then in the Select window select only the Front spoiler and select all points that you wish to align with the Mudguard.
Select a row of points that need to be moved
Then press and hold the Shift key, go to the Select window to add the Mudguard object to your selection. This makes points of the Mudguard object selectable (because it is in Point Edit mode). In the Transformation tab select the Move tool and drag a small box around the fixed point of the Front spoiler and then drag a small box around the target point on the Mudguard.
First drag a box here.. Then one here…
and snap! the two points join at the target point!
This moves the two drag-selected points to the same position. Repeat this for all points where you see fit.
The easiest way to move a single mesh point is to ‘click and drag’. You can also select a point and then use the Move command from the Transformation tab (short key: m ). Make sure all points match the blueprint and are aligned with the other parts of the car. Then you can move all points at the top of the Front spoiler to create a small seam.
Now it is time to finish the Front spoiler object. As mentioned earlier, the air hole is not yet a closed object and we need to close the gap.
We need to close the gap…
Go to Point Edit mode and select two opposite points, like shown in the next image:
Two opposite points selected.. and apply the Merge tool..
Use the Merge command from the tool control bar. This merges the two selected points together to a single point. To close the entire gap you need to keep selecting two opposite points and merge them. If you select all points and then apply the Merge command, you end up with a big mess, because all selected points become one!
Next we need to set the Edge sharpness for several parts of the Front spoiler. So here we go! Have a look at the next image. Select all these edges and set Edge Sharpness to ‘Semi Sharp‘ in the Property window:
Set these edges to Semi Sharp
Select the following edges and set these to ‘Sharp‘ in the Property window:
Set these edges to Sharp!
When you take a look at the reference image, you can see that the glass of the headlights slightly cuts into the Front spoiler. This problem is solved just like we did with the Mudguard. Copy the Front spoiler object and rename it to ‘Front spoiler Glass‘. Go into Face Edit mode, select the corresponding faces (that do not make up the glass part of the headlight in the Front spoiler) and delete these faces. The result is just a few faces that shape the glass part, which cuts into the front spoiler.
The selected faces need to be merged with the Headlight Glass object
These faces form a separate object, which actually should be a part of the Headlight Glass object. So, we will merge both objects. Select both objects (Headlight Glass object first!) in the hierarchy and select the Merge Objects (Merge O) button to make them one single object.
Objects selected… Merge Objects button… Hierarchy after Merge Objects
This concludes the Front spoiler part. This is a good time to save your work
The door
The next modeling task is to create the doors. Because we did the ‘instance trick’ we only need to model one. The approach is similar to the one used in modeling other parts. Therefore we also decided to show many images and little text for this object. Make all objects except the Mudguard Wireframe Invisible. Take a side view. Then start with duplicating the Mudguard and rename the new object to ‘Door_right’. In Face Edit mode, remove all unneeded faces, so you end up with an edge of faces shaped in the profile of the door. Switch to Edge Edit mode and start adding new faces and then use Point Edit to modify the shape to match the blueprint.
Mudguard duplicated and all unneeded faces deleted
New faces created, points edited and moved to match the blueprint in side view.
When the door is modeled in side view, go to a top view to do more point editing and make sure the object matches the blueprint.
Select a vertical row of points and use the red handle to scale the points in position
To model the air inlet, we move and bend the lower edges a little inward (see next image)
Lower edges moved and bent inward
Then it’s time to set the edges to the desired sharpness. Select the edges as shown in the next image, open the Property window and set these edges to ‘Sharp‘:
Select these edges and set Edge Sharpness value to Sharp
And to finish the door modeling, select the edges as shown in the next image and set the Edge Sharpness for the upper ones to ‘Semi Sharp‘ and the lower ones to ‘Sharp‘. That should do the trick for the doors! When done, save your work.
Upper selected edges are semi sharp; the lower edges are sharp…
And that leaves us with showing you the results so far:
The side rear
Before we continue with the Side Rear object, we need to change our blueprint setup just a little. For modeling the Side Rear object you also need to have a blueprint of the rear of the car. This is fixed easily! In the hierarchy in the Blueprint level, select the Front object and duplicate that. Select and rename the new object (called Copy of Front) to ‘Back‘. Then open the Property window for the Back object, at the Col tab and select the appropriate image in the Texture field. Take a side or top view and move the Back object into position.
To create the Side Rear, which is located next to the door, we use a copy of the door. The procedure is the same as we used before. Duplicate the door, rename the object to ‘Side Rear‘ and delete all unnecessary faces. Extrude the Side Rear to match the blueprint and keep going until you reach the wheel area:
The selected edges are extruded… and form the Side Rear as seen from the side..
When you have reached the wheel area, you go to Point Edit mode to make sure all points follow the blueprint.
In point edit mode move the points around to match the wheel area
When done, set the Edge Sharpness like shown in the next image. The yellow lines indicate the edges that must be set to ‘Semi sharp‘; the red lines are edges that must be set to ‘Sharp‘.
Make the yellow edges semi sharp and the red edges sharp.
Take a top view and align the mesh to the blueprint as well. Like before, selecting a vertical row of points and scale them, using the end tip of the coordinate handle will do most of the time.
Before.. and after.. note the red arrow here!
Now continue to model the Side Rear from the top and rear view:
Top view..
Rear view..
Top view…
Rear view
Creating the seam for the Rear Spoiler is easy! Just follow the steps shown in the next five images:
Select these faces and subdivide them once..
Delete the marked face..
Note: the marked face is deleted, to make sure that there are no small areas which may shift in height and later on cause rendering artifacts. So, the face is deleted, and in Edge Edit mode the remaining edge is moved outwards to be aligned with the rest of the faces.
and move the edge to align it..
Then select these small faces… Extrude them downwards and then delete them..
and you have created the seam for the Rear Spoiler!
And this is what we have created up till now (seen from the rear):
Rear view of our Lamborghini so far…
Time to save your work again!
Modeling the Side spoiler
The Side spoiler is modeled using three reference objects: Mudguard, Door_right and the Side rear. Again we use the same procedure as we did before. Duplicate the selected reference objects, then merge the duplicates to a single object, using the ‘MergeO‘ (merge objects) button. This results in a new object at the bottom of the hierarchy in the Select window. Rename the new object to ‘Side spoiler‘.
Selected objects are duplicated and then the duplicates are merged using the ‘MergeO’ button.
Switch to Point Edit mode and delete (use the Destroy button) all points, except the lower row. So you are left with a single row of points. From there we start building the Side spoiler.
Selected points are destroyed, leaving you with a single row of points..
Because the original three objects we duplicated (Mudguard, Door_right and Side rear) were separated by seams, we need to close these seams first before we can continue modeling the Side spoiler. Or else we get these seams (there are two) also in the Side spoiler. The seams are easily found, because there the points are very close to each other. Select the two points (also called ‘vertices’) in a seam area and merge them to a single point. Repeat that for the other seam.
Merge two vertices to a single point using the Merge tool.
From this point the modeling continues in the usual way, creating new edges and align the shape to the blueprint.
Match the blueprint
For the horizontal sides of the Side spoiler, we need to rotate the selected edges slightly to create a slight wedge shape (also see your reference images), like shown in the next image:
Rotate selected edges. Note the use of the pivot point which is located at the side of the Mudguard
Next we extrude extra edges for the air hole in the Side spoiler:
Edges added for the air hole
These edges need to fold to the outside of the spoiler. So, create new edges roughly and use reference images to make the correct adjustments.
The area indicated by the red arrow needs to be closed, point wise (using merge points)
Object closed again (vertices merged)
Go to Face Edit mode, select and extrude the faces just a little bit, like shown in the next view port screenshot. Be sure this time that you set the ‘Leave Floor’ option.
Set the Leave Floor option when extruding selected faces as shown in the next image…
Extrude selected faces
Then you need to close the rear end of the air hole. See next image: this face will not be used and can therefore be deleted:
This selected face can be deleted
Cut the Side spoiler using the Knife tool (not the Object knife!), to add an extra edge.
The selected faces are cut, along the red dotted line, to add an extra edge
Connect the faces from the air hole to the end piece of the Side spoiler. This may require some trial and error to get it really nice.
Connect the selected faces to the end piece
Screenshot of the connected parts
To finish it all, the lower edges are once more extruded and at the front of the spoiler some new faces need to be added to match the extrusion of the lower edges. Also check if you need to change edge sharpness here and there.
Extrude the lower edges
and add some faces to the front side of the spoiler
And this is what we have now, and do not forget to save your work!
Screenshot showing progress until now!
Creating the Roof
Before we start modeling the Roof, let’s have a closer look at some reference images. We scaled the images down a bit and apologize for the decreased image quality. Note that the roof is connected to the Side Rear via small bars. We model from the Side Rear to the roof, so we start with the small bar and then create the Roof. The small bar and Roof are separated by a small seam.
Note the shape and the ribs in the roof structure
Take a top view and duplicate the Side rear object. Select the duplicated object, and delete all edges, except the ones selected in the next image. These edges are used to build the small bar that connects the roof with the Side rear object.
The red lines and arrow indicate the area that needs to be modeled..
Keep adding new faces and make sure the mesh stays aligned to the blueprint. The next image shows selected edges. Set Edge sharpness to ‘Sharp‘ for these edges.
Set Edge Sharpness to Sharp for selected edges
Take a side view, switch to Point Edit mode and align the new Roof faces to the blueprint.
Align new Roof faces to the blueprint
As said before, the transition from the small bar to the roof will be created from the same object. First we extrude two edges to create the seam (see next image). These faces that make the seam need to be destroyed when you have finished modeling the roof.
The arrow points at the seam
Keep on creating new faces and make sure you have edges at every line in the blueprint. This makes aligning the shape to the blueprint easier. Also check in side view if your mesh still aligns with the blueprint.
Align the mesh in side view…
and it looks like this!
Extrude new edges along the dotted line
To prevent any problems when merging the two halves of the car, set the X-coordinate of the last points to zero (0). Use the Property window for that task just like you did when modeling the Hood object.
Set X-coordinate to zero for these points
Just a workflow tip…
If you like to select edges quickly, it sometimes is easier to select points first and then switch to Edge Edit mode!
Select points… and switch to edit edges mode!
To make the Roof object complete, you select all edges on the side and extrude these a little downwards to create a vertical edge. This is similar to all other objects we have created before. See the next few images:
Roof modeled, but not quite finished..
Edges at the rear of the roof are selected and extruded downwards
The first edges are extruded just enough to be able to make a seam
In Point Edit mode adjust the height of the points when necessary
Don’t forget to delete these faces to create a seam!
Select these edges and extrude them downwards and set edge sharpness to ‘Semi sharp’.
Edges extruded to vertical faces and the edges are set to ‘Semi sharp’.
When done, save your work!
The door window frame
Let’s have a look at a reference image that clearly shows how the door window frame is positioned:
Note how the window fits in the door
Now let’s model the door window frame. Basically its an extrude of faces along the lines of the blueprint.
Take a top view and in Face Edit mode select this face as shown in the next image:
Select this face…
Then apply the Subdivide command to the selected face:
Selected face subdivided once…
See next image. The face with the brown color is no longer needed and can be deleted.
Delete the brown colored part…
Switch to Point Edit mode and adjust the points to match the lines in the blueprint. The selected face becomes less wide.
In Point Edit mode, align to the blueprint
When you have aligned the points to the blueprint, it is time to start the extrusion of this face to create the window frame. Switch to Face Edit mode and start extruding the face. Keep switching views, so you can keep the extruded object aligned with the blueprint. You will need to scale and rotate the extruded faces to keep the object in line with the blueprint. Sometimes you even need to switch to Point Edit mode.
Extrude along the lines on the blueprint (top view)
Continue extruding until you reach the Roof. Make the extrusions the same size as the faces in the roof. This simplifies the corrections that you need to do later on. The final positioning for the frame will be done later in the same way as we did with the Front spoiler, using the Move command.
Continue extruding until you reach the roof.
To match the points of the window frame roughly, it is a good thing to select the Roof and set it to Point Edit mode. Now you can see the use of having extrusions the same size as the faces of the Roof. Matching the shape can now be done roughly on sight by moving the points of the Door window frame around.
Points roughly meet the shape of the roof
Now move the points of the Door window frame, until they match the position of the upper point rows of the roof.
Match the upper point rows of the roof!
When done, you should end up with something similar to this (see next screenshot)
This is what it looks like when done! Almost there!
The next reference image shows how the door window frame connects to the Side rear. In real life the frame is cut into two separate objects. We will not create a separate object for this, for the sake of simplicity we will continue to model the frame in one piece.
Reference image shows how the door window frame connects to the side rear
Continue extruding the door window frame. Pay attention to the seam in the roof and match that with the door window frame! See the red arrows in the next screenshot.
Note the seam in the roof!
Just keep extruding until you reach the Side rear object. Then move the points so they exactly match the points of the Roof. Then move the points slightly away from the Roof to create the necessary seam.
Points exactly match the shape of the Roof.
Then they are moved slightly to create a seam.
When we take a closer look at the door window frame, you can see that the frame has a small indentation to make room for the Side Air Flap. So, let’s model this indentation. In Point Edit mode, select the top row of points, starting at the seam, and move them down just slightly.
Top row of points selected…
and moved down a little to create the indentation..
To finish it all off we adjust the curve of the frame just a little so it widens at the end. Time to save your work again!
Screenshot of what we have modeled so far
Modeling the windshield
We start with the windshield. Remember that we only need to model half of it! We start to build the windshield rubber seal first and we build the actual windshield from that. First we duplicate the Roof and the Door_right objects. Delete all faces from these duplicates (or points depending on your edit mode), except the ones on the inside. See next two images:
Delete these points (roof top view) and you need these faces from the copied Door_right object
Note that the copy of the door object and the copy of the roof do not have the same width, so we need to fix that. We will modify the copy of the door object so it gets the same width as the copy of the roof object. Select the copy of the door object and go in Point Edit mode. Then select all the lower points and move them up, so the object gets the same width as the roof object. See next two images:
Select these points of the copy of the door (side view)..
move them upwards, so the object gets the same width as the copy of the roof..
Next, select both the copy of the roof and the copy of the door objects and merge them using the ‘MergeO‘ (merge objects) tool. Rename the new object as ‘Window rubber seal’. The next step is to merge the points in the corner of the former two objects. You may need to move former roof points closer to the corner first. Select the two top points and merge them, then select the two lower points and merge these too. In the Property window set both the Edge Sharpness and Vertex Sharpness to ‘Sharp‘.
Merge corner points, first top ones, then the lower ones..
Now switch to Face Edit mode and select all faces. Check and make sure that all face normals point towards the windshield (thus: inwards). See next image. If face normals point in the other direction, select the relevant faces and apply the Flip tool in the SDS toolbar to make the face normals point the other way.
All face normals point inwards (top view)
All selected faces are now extruded slightly inwards and for all edges the Edge sharpness is set to ‘Semi sharp‘. This finishes the modeling of the Windshield rubber seal object. See next image, showing only the modeled part (not the instanced part):
All faces extruded, edge sharpness set to Semi sharp.
To model the actual windshield object, duplicate the Windshield rubber seal object first. Rename the new object to ‘Windshield‘. Then we model the windshield from the inner edges of the top faces. In Edge Edit mode select all inner edges on the roof side of the Windshield and create new faces as usual and make sure it matches the right hand side of the seal.
Select only the inner edges to model the windshield.. (top view)
Build the mesh and make sure it is aligned to the blueprint in all views..
Now save your project before continuing.
Modeling the side windows and side wing
Modeling the side windows is done in a similar way as we did with the front windshield. Make a copy of the door, delete all unneeded faces and extrude the side windows from the remaining faces. Here we go! Select the Door_right object and duplicate it.
Select all inner faces in the copy of Door_right object.. (rear view)
Press the Ctrl+i keys to invert the selection (all selected faces become deselected and vice versa)..
Delete all currently selected faces and we will build the side windows from the remaining strip of faces. The faces of the strip are slightly extruded downwards. Rename this object to ‘Side window seal‘
This is where we will build the side windows from: the Side window seal!
Duplicate the Side window seal and rename that to ‘Glass_Door_Right‘. Select all outer, lower edges and extrude these downwards.
Outer, lower edges extruded downwards
Use the Coordinate handle to scale the bent edges to a horizontal line. When done, the profile faces that shape the Side window seal can be deleted from the Glass_Door_Right object.
Scale the bent edges to a horizontal line
Now take a top view and modify the edges of the door window. The lower edges have been scaled a bit and also rotated just a little. You can use the coordinate handles and the rotate handles for that. If these handles are hidden, you can get them back via the Property Window – Wire tab.
Edges modified
Because the window is slightly bent outward in the real car, we add an extra edge to the Glass_Door_Right object. This allows us to also make the window bend a little. Take a side view and cut these faces as shown in the next image:
Cut the faces to add an extra edge (side view).
Go to Point Edit mode and move all the new points you just added slightly outwards, except the one most left and the one most right. The points at the far left and far right remain in position, because they are close to the window seal.
Perspective view: the new points are slightly moved outward
Take a top view again and shape the lower part of the object:
Top view: object now in position
Because we had no Glass_Door_Right object yet, we could not yet fully model the Side Rear object. Now we can complete the Side Rear. Select the Side Rear in the Select Window. Go to Edge Edit mode and select the lower edges as shown in the next image:
Select these edges…
And extrude these two times and use the rotate tool (or point editing) to match these edges to the Glass_Door_Right object.
Top view: new edges added to the Side Rear to match the window.
And another screenshot, showing all from the side in perspective projection:
And in perspective projection…
Now for the easy part! The blinds are created from a duplicate of the Glass_Door_Right object. Rename the duplicate to ‘Blinds_right‘.
In Face Edit mode simply delete the unneeded faces. This leaves you with this:
Window object copied, unneeded faces deleted
Next, select all the faces of the Blinds_right object and slightly extrude these outwards.
Faces extruded outwards…
Set Edge Sharpness and Vertex Sharpness to ‘Sharp‘ in the Property Window – Spec tab.
Edges and vertices set to sharp!
Finally adjust the shape of the blind next to the last window to match the blueprint. You can use Edge Edit mode or Point Edit mode for that.
Adjust the blind to match the blueprint!
When ready, you can delete the faces of the Glass_Door_Right object which are covered by the Blinds_right object.
The next and final part in this chapter is the Side Wing. The approach for modeling is again the same. Duplicate the Side Rear object and rename the copy to Side Wing. Then delete all faces you don’ t need and you end up with this:
The beginning of the Side Wing
Go to Face Edit mode and start extruding, until you match the blueprint (see next image):
This where the Side Wing ends
Then to finish it, adjust the Edge Sharpness which should lead to something like this:
It really looks like a car already…
And again, it is time to save your work before continuing.
h2>Modeling the wheels
It’s about time to give our Lamborghini some wheels. So let’s model one, which of course you can duplicate three times :-) We start with a reference image and will map that reference image on a rectangle. Create a rectangle (can be Analytical) and parallel map the reference image on it. To create a perfect square rectangle, just press and hold the Shift key, while creating the rectangle. Scale the rectangle to the proper dimensions, so it covers the wheel in the blueprint.
The used reference image (scaled down to 60%)
Reference image mapped on the rectangle, scaled down and set in position
First create a new level called ‘Wheel‘. Then start with the profile (as seen from the front of the car) of the metal part of the wheel. Because your reference image is only 2 dimensional, you have to use your imagination a little to get this done. We use the NURBS curve tool to create the profile curve in front view. Remember that you need to click two or three times in the same place to create sharp corners! More clicks means sharper corners, but more then three points at the same place is useless ;-) When done, rename the curve to ‘Profile‘.
Profile curve of the wheel… Detailed view of the seam in the wheel
Take a front view and create a new horizontal two points NURBS curve, which will be used as a rotation axis for the profile curve. To create a perfectly straight curve, start the NURBS curve tool, click to enter your first point, press and hold the Shift key, move the mouse horizontally and click again. Move the rotation axis to the centre of the wheel. When done, rename this curve to ‘Axis’.
Rotation axis added (perspective view)
Now we will rotate the Profile curve around the Axis. First make sure the profile curve is perfectly positioned at the top of the wheel, or else the wheel gets distorted. To do this, first select the Axis (in the Select Window), press and hold the Shift key and then select the Profile. Next, apply the Rotate tool from the NURBS tool bar. Before accepting the Rotate tool, set the Resolution to 12:
Rotate tool activated, Resolution set to 12
Accepting the tool creates the basic outer shape of the wheel. In the Select Window a new level is created, called ‘mesh..‘. Inside that level you will find both the profile curve and the axis curve. The good part is that you can now edit the shape of the profile curve and the mesh will immediately adjust to show you the new shape. So you can tweak the shape until you are satisfied with it.
After applying the Rotate tool you have the basic shape of the wheel
Next, create a 12 point NURBS circle, which has the same radius as the inner side of the wheel.
A 12 point NURBS circle added (the red circle inside the wheel)
In the Select Window, duplicate the red NURBS curve, and size the duplicate curve down. Use the Size tool and also check the ‘About Pivot’ option.
Size tool activated, About Pivot option checked..
Make it just big enough to contain the inner wheel screws. See next image. Remember that the order in which you created the curves here is important. So a new curve should always be at the bottom of the hierarchy. The importance of this will be shown later.
The inner NURBS curve added…
Select both these curves in the same order you created them and apply the XSect tool from the NURBS toolbar. Use default tool settings. The result is that the space between the selected curves is closed. A new level, called ‘Mesh’ is added to the hierarchy in the Select Window. Rename this mesh to ‘Wheel plate‘. Change the view and check if the wheel plate mesh is correctly positioned and move it into position when necessary.
The space between the two curves is closed using the XSect tool
Now select the inner NURBS circle inside the Wheel plate mesh, duplicate it and make it just a little smaller (see next image). Then take the inner circle, duplicate and resize that, so it has just enough space for the centre axis of the wheel. Move the small circle just a little inwards (when seen from the side). Because these NURBS circles are also in the Wheel plate level, the shape of the mesh remains closed and a small cone is created at the centre of the wheel.
New NURBS circle added, and moved a little inwards..
Make all the current wheel parts wireframe invisible (WF Inv), so we get a clear view window and have room to model the other details on the wheel. As we can clearly see on the reference image, the wheel plate contains five larger ‘air holes’. In the Wheel level, create a new NURBS circle (12 points will do) that has the size of one of these large air holes in the wheel. Make sure your circle does not touch the outer rim of the wheel (see next image).
Rename your circle to ‘large hole‘.
New NURBS curve added to model one of the large holes..
To cut a hole in the wheel plate mesh, we use the Trim tool. The Trim tool icon is located at the far right of the NURBS toolbar. You may need to drag the NURBS toolbar a bit to the left to see the icon.
The position of the Trim tool
Using the Trim tool is easy. Select the ‘large hole’ circle, press and hold the Shift key and then select the Wheel plate level. Click the Trim icon and accept the tool. The NURBS circle is cut out of the Wheel plate mesh, leaving a nice hole. Also, after applying the Trim tool, a new object is added to the hierarchy. This is a so called ‘trimcurve‘. This curve defines where the wheel plate mesh is cut. Deleting the trimcurve from the hierarchy immediately restores the wheel plate mesh to its original state.
Trimcurve added to the hierarchy
Because the Trim tool created the trimcurve inside the mesh level, we can now move our original NURBS circle to a new position and repeat the process. The Trim tool will add a new trimcurve to the hierarchy every time. This allows us to create the other four holes easily.
All holes created with the Trim tool
Working with trimcurves can cause an unexpected problem, which leads to terribly deformed meshes. The trimcurve has to lie within the UV space of the mesh (as mentioned in the RS user manual). See next image: It is not allowed to put circle B across the line between the starting points of the circles that define the cross section mesh. The starting point looks like a small triangle on both the outer and inner rings of the mesh (see arrow in next screenshot pointing at the starting point of the outer ring). If you break this rule, your mesh gets deformed! If this occurs, select the trimcurve in the hierarchy that causes the problem and open it’s properties at the Spec tab. At the bottom of the Property Window, check both the Wrap U and Wrap V options and the deformation problem should be gone!
It is not allowed to put circle B across the line between the starting points of thecircles that define the cross section mesh.
Set the Wrap U and Wrap V options!
Later on we will add some more smaller holes to the mesh for the wheel screws. For that we will also use trimcurves and we know there is a good chance you will get into troubles at that point. The troubles again will be caused by the starting point of the mesh. Only this time the Wrap U and Wrap V options are not going to be much help, because later on we will use these smaller trimcurves in combination with the Weld tool. When the Wrap options are checked, the Weld tool does not work properly. So, we need to plan ahead in this case. As you may know, you can also change the starting point of either the mesh or the curves afterwards. The disadvantage of that solution is that it also affects on the holes you already made: they will change shape and position. Not what you want ;-) Have a look at the next image, that shows how the starting line only crosses the large hole, but not the smaller one. This is what we are aiming for eventually:
Starting line only crosses the large hole, not the smaller ones!
To give the ‘air holes’ the proper shape (also see reference image at the beginning of this chapter), we need to build 3D cylinder shaped objects from the curves. The process is simple: duplicate NURBS circle, scale, move a few times and finally apply XSect to create a cylinder shape. Each cylinder will consist of four circles. Then we will use instances to create 4 more cylinders. Here we go:
Go to wireframe display.Select the ‘large hole’ circle in the hierarchy, press and hold the Ctrl key and drag the red transformation handle a little forward to duplicate the circle. Select the duplicate circle (called ‘copy of large hole’), duplicate that again (use the Ctrl + d keys) and resize this copy: make it just a little bigger. Select the second duplicate curve (now called ‘copy1 of large hole’), press and hold the Ctrl key and use the red transformation handle to move that a little backwards again. This again creates a new circle, called ‘copy2 of large hole’. Now we have 4 curves. Multi select these in the order they were created, select the XSect tool again, set the Closed option and accept the tool. A cylinder shape is created. Also a new mesh level containing all 4 curves is added to the hierarchy. Rename the mesh level to ‘cylinder’.
XSect tool selected with the ‘Closed’ option set..
Now move the cylinder to the hole which we previously cut out from the Wheel plate mesh. To prevent render errors, we need to scale the cylinder down just a tiny bit, so that the trimcurve is between the inner and outer cylinder walls. See next image: the red arrow points at the trimcurve (dark red color).
Trimcurve (red) inside the cylinder (white)
Instances used to create the other four cylinders.
With the cylinder created, it is easy to create the other ones using instances. An instance is created as follows: select an object, press and hold the Alt key and drag one of the objects transformation handles. Now you have an instance, which basically is a very memory efficient copy of an object. We created all the instances from the original cylinder object. To create the holes for the wheel screws, we perform the same procedure as for creating the air holes. Create a NURBS circle, rename it to ‘wheelscrewhole’ and use the Trim tool to cut holes in the ‘Wheel plate’ object. Note that you do not need to create cylinders, only holes. When done, you may want to save your work now!
The hierarchy so far… New hierarchy with screw holes…
The holes for the wheel screws added…
The holes for the screws are shaped like cylinders pointing inwards. So we use the same procedure like we did for the air hole cylinders to add the cylinder shapes. Here we go. You may want to set the outer mesh, the cylinders for the air holes and the instances to WF Inv to clear the view.
Select the NURBS circle, used to cut out the first wheel screw hole (we called it ‘ wheelscrewhole ‘). Make sure it is positioned a little behind the first screw hole you created in the Wheel plate (so, it’s at the rear side of the wheel). Duplicate that NURBS circle and move it a bit backwards. Multi select both circles and apply the XSect tool. This creates a hollow cylinder and adds a new mesh to the hierarchy (see next image).
New cylinder added to the hierarchy.. The cylinder added at the rear side of the wheel..
Create four copies of this cylinder and move them in position behind the other wheelscrew holes. To close the gap between the wheel plate and the cylinders we will use the Weld tool. The weld tool will add a so called Weld object to the hierarchy. Make sure the cylinders are not too far away from the trimcurves. In the Select window, select the trimcurve (in our example ‘ trimc53’ ) and then multi select the cylinder (in our example called ‘ mesh9’ ).
Mesh and trimcurve selected.. Note the gap between the cylinder and the Wheel plate..
Click the Weld tool and in the Weld tool control bar set both ‘Size1’ and ‘Size2’ to a value of 0,05.
Weld tool selected and its options set..
When you now would accept the tool the weld would probably not look good. You see a twisted mesh added to your scene. This is easily fixed before you accept the tool!
A nasty twist in the mesh!
To fix the twist you have to tell the Weld tool which parts of the meshes need to be connected. Turn the view cam so you can see the cylinder from the side and press and hold the left mouse button and draw a line as shown in the next image. Make sure you stay inside the boundaries of the cylinder. Then rotate the view, so you also can see the wheelscrew hole and draw a second line as indicated in the other image. Then accept the tool. Repeat this process for the remaining wheelscrew holes and cylinders. Then save your work!
First draw a line here… Then here and then accept the Weld tool.
Just one more detail to fix. If you look closely to the reference image at the beginning of this chapter, it is clear that the air holes are not complete circles. This effect is easy to do. Just slightly tilt (rotate) the cylinders and move them into the outer rim of the wheel, so the wheel covers part of the cylinder. See next images:
Slightly tilt the cylinders in the direction of the blue arrow…
Then move them into the Wheel plate..
When done you can render an image that looks like this:
The wheel completed.. let’s move on to modeling the tire!
Now save all your hard work before continuing!
The Brakes
When you take a look at the reference image of the wheel (beginning of this chapter), you can clearly see the Brakes (basically a disk with many small holes in it). We are going to use analytics, instances and the Macro recorder to build one. You can build the rest of the details yourself then ;)
Make sure you saved your previous work, so you can clear the view window and start fresh. Take a front view and create an Analytic Cylinder and rename it to ‘Brake‘. Make it not too thick. The brake is punctured with many smaller holes and all these smaller holes are made in series of five. We will create these smaller holes using one small analytic cylinder and four instances of that cylinder. Create a small cylinder at the rim of the Brake (at the 12 o’clock position) and rename that to ‘small hole’. See left side image.Take a top view and extend the small hole cylinder, so it sticks out on both sides of the Brake cylinder. (see right side image for top view).
Brake disk and a small cylinder at 12 o’clock position Top view (it sticks out on both sides of the Brake cylinder)
Then, just like in the reference image add four more instances (not duplicates!)of the ‘small hole’ and place them diagonally below the first one. When ready, drop the small hole and its instances in a level (select them and press the ‘d’ key)
Instances added and positioned diagonally… your hierarchy looks like this..
Now for the magic… Press the F8 key to invoke the Numeric Window. Select the small hole level (the one containing the instances) and from the top menu bar select Macros -> Record (Ctrl + m). This starts the Macro recording mode. All actions taken from here are recorded and can be played back later. Select from the top menu bar Edit -> Instance. A new instance of the ‘small hole’ level is added to the hierarchy. Select this new instance level, click the Transformation tool tab and click the Rotate icon. Click at the center of the Brake cylinder, click again at the cylinder called ‘small hole’. Now the Rotate tool is activated. Move the mouse pointer to the Angle field in the Numeric Window and enter a value of 30. This rotates the instanced level 30 degrees around the center of the Brake, counter clockwise. Select Macros -> Record (Ctrl + m) again to end the macro recording. Now, with the new instance level still selected, press Ctrl + g toexecute the current macro (the one you just recorded). Another instance with five holes is added to the hierarchy. Keep on repeating this macro, until you have created a circular pattern of small holes. See next image:
All small holes created using instances and a macro!
Almost there! Select the small hole level and all its instances and again drop these to a level. Your hierarchy looks now like shown in the next right hand image. Then multi-select the original Brake cylinder and the small hole level (containing all the instances!) and perform a Boolean Remove. After that your hierarchy looks like shown in the center image. A test render shows the Brake cylinder after the Boolean Remove.
The hierarchy before Boolean Remove…. and after…
and here a test render with the results.
Now select all the brake related components and drop them into a level. Position the brake cylinder inside the wheel and scale it to the proper size. You can now of course add more details like rings and screws, if you like. We are moving on to the next chapter, the tires.
Modeling the tires
Before we start modeling we take a look at some reference images, like these:
Look at the pattern of the profile on the tire.. also note the decreasing depth at the side!
We take the second image and use that as a background image for our modeling process. Make sure you have saved the Lamborghini project so you can clear the scene and start a new one. In front view, create a square analytical rectangle (press and hold the Shift key while creating the rectangle to make a perfect square), open properties at the Col tab and set the reference image as texture for the rectangle. Then go to the Wire tab of the properties and set Texture quality at 512 or better. Make sure you are working in OGL display mode, so you can see the texture on the rectangle.
Next, create a polygonal SDS Rectangle and place that at the centre of the tire. Like always, we model half and create the other half using mirroring. Switch to Face Edit mode and select the face. Then use the Knife tool (the one next to the Dupl. E tool), to add eight (8) vertical edges in total. Each edge creates a new face, which we later use for the profile of the tire. To get a nice vertical edge set the following options and press and hold the Shift key before you click to finish the tool:
The Knife tool and the options you need
Remember that you can use the Again function (press right mouse button in the View window and select Again from the pop-up menu, or press the ‘a’ key) to repeat the tool with the same settings as before.
For the position of the rectangle and the vertical edges see the next image:
Eight vertical edges added with the Knife tool
Repeat this process to add six more horizontal edges, like shown in the next image. To add the edges, you first need to select all faces you wish to cut. To get the same view as in the next image, select the SDS rectangle, open Property window at the Wire tab and set the ‘No shading‘ option.
And six more horizontal edges added…
Then start moving points around, to roughly match the profile of the tire:
Profile roughly matched
The next step is to select all faces that need to be extruded downwards (the grooves in the profile). Switch to Face Edit mode, select the required faces and extrude these downwards. In the next screenshot you can see which faces you need to select (they all have a red dot):
Select all these faces and extrude them downwards..
Next, delete all faces that cross the profile grooves. See next image to see the faces you need to delete:
Delete selected faces as shown here
Also, delete the faces that are on the inner side of the tire, like shown in the next image:
Also delete these faces
Switch to Edge Edit mode and move the lower, outer edges up, like shown in the next image:
Move lower outer edges upwards
Here is a screenshot showing the result of the last instruction (front view)
Front view of the profile
Switch to Point Edit mode and bend the profile a little, like shown in the next image:
Front view of the adjusted tire profile
Select all the edges at the side of the tire and start extruding them to add new faces. Remember: select the edges, press and hold the Ctrl key to add new faces!
Select these edges and add new faces
The grooves in the profile now should be getting less deep. Switch to Point Edit mode and move the points that make the grooves. Level these points with the other ones. Where two points come together, use the Merge tool to join these into a single point.
Points of the grooves leveled and merged with the other points
Now the profile is reduced to zero, you can extrude the faces like you did before in Edge Edit mode:
Now extrude these edges downwards to make the side of the tire
Next screenshot shows the profile in front view after adding some faces:
Front view of the tire we have created so far..
Now it is time to set Edge Sharpness for the edges. Take a look at the next image to see which edges should be set to ‘Sharp‘; the other edges will keep the default edge sharpness.
All selected edges should be set to ‘Sharp’
Now you can build the actual tire from the part you just created. Duplicate the object you now have and move it down and see how they fit together. Probably you will have to do some tweaking to match the two pieces together. When tweaking, remember to move the points in pairs to keep the groove width intact:
Duplicate added.. Tweaking done!
OK, after the tweaking is done, delete the duplicate object. Now the original object is ready to be duplicated and you can be sure the duplicates all fit together! Duplicate the original (adjusted) object again. Move the duplicate down and make the two objects touch. Then select both objects and apply the ‘MergeO‘ (Merge Objects) tool. The two objects become one in the hierarchy and get the name of the first selected object.
Now save your work!
Next, in Point Edit mode, select all points at the intersecting area of the (former) two objects. See next screenshot:
All points at the intersecting area selected
Then apply the ‘JoinF‘ (Join Faces) tool. In the tool control bar, set the Distance parameter to a small value (actual value depending on the distance of the two objects, the value shown in the screenshot may not be accurate for you). All faces whose edges have a distance smaller then the value you have set, will be connected. If you set your distance parameter too large, you may end up with more faces joined then you would like. So experiment with some values and make a simple test render. If the results are OK, then save your work. If not OK, then undo your last actions and try again.
Join Faces tool selected, Distance parameter set..
Repeat this process four times in total. The duplicated object doubles in size every time, so the profile object grows fast! You’ll end up with a long string of profile parts all joined together. Then of course you have modeled only half the tire. A duplicate of this object will be used and mirrored. Finally they will be merged to make the tire complete:
Half a tire modeled then mirrored and merged
The last step is to apply the Bend tool (it is in the Transformation tab). Make sure you are in Face edit mode and select all faces. Press the F8 key to invoke the Numeric Window. Take a side view and start the Bend tool. Drag a box around the most left side of the object and then one around the most right side. Then simply enter 360 in the Angle field of the Numeric Window. The profile of the tire will bend perfectly.
Bend tool in the Transformation tab
enter 360 in the Angle field
This is the final result after bending the profile:
Bend tool applied!
When done bending, the final step is to adjust the size of the tire, to match the size of the wheel and we are ready! Then duplicate the entire wheel three times to create 4 complete wheels, save your project and your car is ready to roll!
Test render of our wheel
Lights please!
In this part we add some detail to the car model. We will model the inner parts of the headlights. If you have created the wheels as a separate project, reload the Lamborghini.To make clear what we are modeling here, we show a nice render of the end product:
This is what we will be modeling
Start with creating a SDS rectangle that has the same shape as the Headlight Glass object. Before you start, make sure you set all of the car objects ‘WF Inv‘ (wire frame invisible) except the Headlight Glass object. In top view, create a SDS rectangle, using the Subdivision tool. Set the Type to ‘Polygonal‘ and leave the other parameters at their default values, as shown in the next image:
The Subdivision tool selected, all options set
Use the Headlight Glass object as a template. Use all four corners, so the shape of the face you create has the same dimensions as the Headlight Glass object. After four clicks a new SDS face is created. Then click ‘Accept‘ (or select Accept from the Right Mouse button pop-up menu) to finish the tool. A new object is added to the hierarchy.
Four clicks and you have a new SDS face
The face now has a rather rigid structure. To fix that, we need to apply the Smooth tool from the SDS toolbar.
The smooth tool in the SDS tool bar
Select the SDS object in the Select window, apply the Smooth tool two times, to divide the large SDS face in more smaller faces.
Smooth tool applied twice
The object now consists of 16 faces. To make room for the actual light sources, we need to transform the face into a box which has no top lid. Take a front view, select all faces and apply the Extrude tool from the SDS tool bar.
The Extrude tool
After the extrude you get a hollow box with no top lid, which is exactly what we need to continue.
Extrude applied to all selected faces
Now apply some point editing, so the box fits into the Mudguard. Take a close look at the next screenshot, because this is what you’re aiming for. Note that the corners of the object all have different heights and the box now gets more or less shaped like a ‘ wedge with a twist’. Rename your object to ‘box’
The box is now ready
It is time to start modeling the shape of the space for the light sources. This will be ‘Booleaned‘ out of the box. Start with a SDS cylinder. Use point editing to taper the last 3 rows of points of the cylinder a little bit (no sharp point, just taper the shape a little). Then place the cylinder so it overlaps a little at the rear of the box.
The cylinder overlaps at the rear of the box
Carefully move the cylinder in position. Note it sticks out on all sides, like shown in the next screenshot:
Cylinder in position
Select the box, press and hold the Shift key and then select the cylinder. Apply the Boolean ‘Remove‘ from the Boolean menu to cut out the cylinder shape.
Apply the Boolean ‘Remove’
The Boolean removes the cylinder from the box. Then after the Boolean operation, select the Box in the hierarchy and open the Property Window at the Gen tab. In the Volume section, set the ‘Volume inverted‘ option. For the cylinder the ‘Volume inverted‘ option and the ‘Paint in Boolean Operations‘ option must be set. The next screenshot is a render, because the OGL display of Booleans is not accurate enough to properly show you what happens. The cylinder is cut out and also filled with new faces in the box:
The box after the cylinder has been removed (test render)
We need to cut out a second cylinder, which is also a little bigger. You can use a duplicate from the first cylinder. Open the Boolean level you just created. Now select the cylinder and duplicate it.
The second cylinder is a copy of the first one
Note that all objects inside the Boolean level are Wireframe Invisible (the names of the objects are written in Italics). Uncheck the WF Inv flag for the duplicated cylinder, so you now can easily move that one a little to the left (or right, depending where you cut out the first one). Then slightly increase it’s size. When done, make it WF Inv again. If you now test render the scene, you will see that the Boolean operation also works for the second cylinder.
Two cylinders cut out from the box
As you can see in the reference image at the beginning of this chapter, the lights are partly covered. We will now model this cover. Create a SDS rectangle with a U value of 10 and V value of 2. Rename the object to Cover.
SDS rectangle with a U value of 10 and a V value of 2.
Use point editing to match the shape of the box. See next screenshot:
The cover matches the shape of the box
Next use some point editing to create some room for the second cylinder (also check with the reference image):
A small cut created using point editing
We must not forget the space for the Indicator Light. Go to Face Edit mode and select all faces of the cover and apply the Knife tool (see next screenshot). Then select the two faces at the left side (with the red dots in them in the screenshot) and subdivide them. While subdividing, use the ‘Groups‘ option:
Select the Groups option for the Subdivide tool!
Extra edge added. Faces selected and subdivided, to create room for theIndicator Light
The two faces are then Extruded downwards and slightly rotated:
The Indicator Light created
To give the Cover some depth, select the edges as shown in the next image and extrude these a little bit downwards, like you did before in earlier steps in the tutorial.
Select these edges and extrude them downwards just a little bit
Next detail is a small hole on the right side of the cover object. in top view, subdivide the face once, as shown in the next image. Then use point editing to move the points so they form a nice square. While point editing pay attention to the face that the cover object is not perfectly perpendicular to the view. This shows immediately when you move the points, because the surface starts to buckle. Simply take a side view, or front view to correct any errors.
This is where the hole comes; face subdivided, points moved to form a square
Next extrude the square face inwards and move it a little backwards to create the hole we need. The cover is done, time to save your work!
Face extruded inwards creates the hole we need
Now for the next part, the spot lights. They are made out of three parts. These are simply sets of NURBS circles, which are skinned using the XSect tool. We create two separate objects (a rear end and a front end), because that is easier with texturing later on. When you have created the first spot light, duplicate it and resize it, so you have one bigger and one smaller spot light.
To start with the rear end: in Front view, create an 8 point NURBS circle, duplicate it twice and move the curves away a little. Select the first two curves and apply the XSect tool from the NURBS tool tab. A cylinder is created. In the hierarchy a new object called ‘Mesh..’ is added at the bottom.
Now for the front part: select the third curve and duplicate it. Move the duplicate (the fourth circle) a little, Then duplicate that one as well. Select the fifth circle move it away and size it down just a little using the Size tool in the Transformation tab. When applying the Size tool, also set the ‘About pivot‘ option. Then, once more, duplicate the fifth circle, size it down again, just a little and move it inwards, into the spotlight. Repeat the last step again for the 7th circle. Then, select circle 3, 4, 5, 6 and 7 (in that order) and apply the XSect tool and this is what you get (see next image):
Seven NURBS circles skinned to create the spot light
Now for the easy part: add a NURBS sphere and size it, so it fits in the opening at the front. Move it into position and you’re done!
NURBS sphere added and moved into position
One more detail to fix: one spotlight is just a little bit bigger then the other one. The one directly under the Indicator light is the smaller one. Select it and size it down just a little bit and our test render of the completed headlight looks like this:
A render of the completed headlight
And don’t forget to save your work before you continue!
Mirror mirror
Another detail that needs to be added is the side mirror. An easy object, compared to what you have modeled up till now.
Make sure you are in OGL display mode and in parallel projection.We start with a Polygonal SDS cube in top view. Note that you need a V value of 3 while creating the cube!Rename the object to Side mirror.
Polygonal SDS cube selected
Then switch to Point Edit mode and move the points around until you have the following shape (see next screenshot):
Polygonal SDS cube after point editing
Then switch to Face Edit mode and extrude the face as indicated in the next image. Then switch back to Point Edit mode and adjust the shape, so you get something similar to this:
Face extruded, points moved
Go back to Face Edit mode and extrude this face again two more times. Select all faces, take a front view and apply the Knife tool (not the Object Knife!) two times, to add horizontal edges, as shown in the next image:
Horizontal edges added with the Knife tool (perspective view)
Now select the two opposite faces as shown in the next image and apply the Tunnel tool.
Select these opposite faces… and apply the Tunnel tool
The result is a hole in the object. The Tunnel tool added faces at the inside of the hole. This prevents that the object looks hollow, when viewed from the side. Now destroy the outer face, which is marked with the dotted cross. This reveals another face, destroy that one too, so you get this:
Tunnel tool applied, remaining two faces destroyed
Next we need to increase the face count, so we can add some rounding to the object. This time we will use the O.Knife tool (Object Knife) in the SDS tool bar. The tool requires to have an object to cut with. This time, that will be an extruded SDS object. So, create a SDS rectangle and add new faces using the same technique as you have been doing throughout this tutorial. Make sure the new object sticks out both on the upper as well as the lower side of the mirror object. Shape it, position it and use point editing to make it look like the object shown in the next image.
Cutting object added to the mirror
Now select the Mirror object, press and hold the Shift key, then select the cutting object you created. Click the O.Knife icon and accept the tool. Delete the cutting object from the hierarchy, because it is no longer needed.
Edges added with the Object Knife tool
Next we add some more detail to our mirror. Switch to Edge Edit mode and select one edge from third edge row from the left. Press and hold the Shift key and apply the Loop tool to select the entire ring of connecting edges. Then apply the Bevel tool to create a set of small faces (see next image):
Ring of edges selected, Bevel tool applied
Switch to Face Edit mode to automatically select all faces in the ring. Now extrude these faces inwards:
Ring of faces extruded inwards
Now we need to make room for the actual mirror glass in our mirror object. Select all faces that make up the part where the mirror glass should be. Subdivide these once. While subdividing, set the ‘Region‘ to ‘Groups‘ and you get this:
Faces selected and subdivided group wise
Now extrude these inwards and you get this:
Faces extruded inwards
The final step is to add some rounding to our mirror object. Switch to Point Edit mode and select these points (see next screenshot). The easiest way to select them is to take a top view and drag select all back edges. Then take a front view select the Extend tool, which is located in the Transformation tool tab. Click in the centre of the mirror object, then press and hold the Shift key, move the mouse up (a nice straight line appears), click again, then move the mouse back down slowly and watch the movement of the selected points. When happy with the results, click again to finish the tool.
Points selected and slightly moved with the Extend tool
All that is left to do is add this object to the Lamborghini, maybe scale it down to the proper size and save your work!
Rear window and rear Louvre’s
Let’s have a look a reference image that clearly shows the Louvre’s covering the rear window.
Reference image
We start with modeling the Louvre’s and then add the rear window.
As usual we use one of the car parts we already modeled and duplicate that. This time we duplicate the Roof object and rename that to ‘Louvre-Frame’. Select the edges as shown in the next screenshot:
Select these edges
Extrude them downwards and then select the newly created faces:
Select these faces
Then select Edit -> Invert Selection from the menu bar (or press Ctrl + i), to deselect all selected faces and vice versa. Then delete all selected faces.
Invert selection.. delete the selected faces and you get this..
Now switch to top view and create a new SDS rectangle. Rename this rectangle to ‘Louvre‘
Rectangle added
In Edit Points mode, the vertices in the corners are moved to match the blueprint. And because the Louvre is slightly bent, add two vertical edges (and thus also two vertices) with the Knife tool and then again align the shape to the blueprint.
Edges added with the Knife tool
Now apply the Extrude tool two times to add some depth to the Louvre’s object. Use the following tool settings:
Extrude tool settings
Remember you can use the Again function from the pop-up menu in the view window, to repeat the tool with identical settings.
After the second extrusion, select the middle edge (as shown in the next image) and slightly move it just a little bit outwards. This creates a nice smooth rounding which is important for the correct light reflections later on.
Select this edge and move it slightly outwards
Then select all outer edges (upper and lower horizontal and vertical edges) and set the Edge Sharpness to ‘ Sharp‘
Select these edges and make them sharp
Next, switch to Edit Points mode and make sure that the inner points of the Louvre are exactly at the mirroring axis of the car. Also make sure that at the vertical edge between the two arrows there are no more vertical faces. If there are, you can remove them:
These points must be at the mirroring axis
To create the remaining Louvre’s we only need to create instances of the original Louvre. Press the space bar and make sure you are no longer in edit mode. Take a top view, select the Louvre object, press and hold the Alt key and drag the green transformation handle in the View window to create a new instance. You need to add three instances in total. The biggest advantage of using instances is that they require less memory. When done, move all objects to the Lamborghini level in the hierarchy in the Select window.
All Louvre’s created (mirrored objects also visible)
Then move each of the Louvre’s into position so they are all aligned with the roof structure:
All Louvre’s in position
Now it’s time to model the rear window. We use another SDS rectangle for that. In top view, create a SDS rectangle:
SDS Rectangle added
Rename the rectangle to ‘Rear Window‘ . Then switch to side view and adjust the position of the Rear Window. It must be rotated slightly and then moved just under the Louvre’s:
Rear Window moved and rotated into position
And we’re done! Save your work before continuing with the next chapter!
The rear bumper area
Before we start modeling the rear bumper area, let’s take a look at some reference photo’s first:
Note how the tail pipes fit in the bumper area
Note the transition from Side Rear to bumper area
We start with a duplicate from the Side Rear object and start modeling from the rear wheel area. Rename the new object to Rear Bumper. Delete all the faces you don’t need and move the Rear Bumper slightly to create a seam.
This is what we start with (all unneeded faces deleted)
Start extruding as usual and keep the mesh aligned with the blueprint in side view and rear view:
Extruded and aligned with the blueprint from the side.. and from the rear
Next select the points as indicated in the next image. Then switch to Edit Edge mode and start extruding sideways. Please note that the first edges make a seam, so just move them just a little (a few mm), then resume the extruding as usual.
Select these points.. and extrude sideways..
Then we need to add some faces at the top of the bumper. These faces also stick out a bit (also check the reference image).
Seen from the rear and from the side
Next we need to create a small seam. Select the face as shown in the next image:
Select these faces and extrude them slightly inwards to make a seam
The faces that are at the inside (and are still selected) are no longer needed and can be destroyed. This way you create the seam:
Selected faces can be destroyed
For the details you sometimes need to check the reference images because the blueprint is not detailed enough in some areas. Here is a screenshot of an almost finished Rear Bumper:
The almost finished Rear Bumper
And here’s another one. Images say more then a thousand words!
Note the detail at the tail pipe area!
Next, go in Edit Edge mode and extrude the two edges together as shown in the following image:
Select these edges and extrude them upwards
Then switch to Edit Points mode and move the point (vertex) to the adjacent face as shown in the next image:
Move the vertex to join with the adjacent face
Extrude the object until it looks like this (the arrows show points of interest). Note that the pointy shape has an extra set of faces compared to the previous image and also note that there are some extra horizontal edges added to the two extruded faces. Finally select the top left edge and extrude it, to add a small flap and repeat that with the top right edge.
This is what we aim for
Now take a top view and compare your object with the blueprint. You need to align it with the blueprint. Switch to Edit Points mode to make the necessary adjustments. Pay attention to the two flaps you created. See next two images:
Top view before aligning with the blueprint
Top view after aligning with the blueprint
Now let’s continue with the rear view. The two flaps are now clearly visible. Take a good look at the reference image at the top of this chapter again. The left flap points straight up, the right flap is bent forwards slightly. This face will is where the license plate will be.
Note the position of the two flaps
The next image shows that the area between the two flaps is open. This gap needs to be closed. We will use the Subdivision tool, which is in the SDS toolbar. Start the Subdivision tool, press and hold the Alt key and close the lower area in the gap with a 3 sided face and close the top part of the gap with a 4 sided face. When done, check the face normal. If it points in the wrong direction, use the Flip tool to change the direction of the face normal.
The gap is open.. Three sided face added..
Gap closed with a 4 sided face.
Finally extrude the edges on the side, until you reach X coordinate 0,00. This closes the rear bumper area.
Rear bumper area finished.
And the next image shows what we have modeled so far!
This is what we have modeled so far!
Save your work before continuing.
Grille’s and Taillights
Before modeling the grille’s and the taillights we first take a look at a reference image, like this one. Focus on the black grille’s and the tail lights, because we are modeling these in this section of the tutorial:
Nice reference image of the rear grille’s of a Lamborghini Murcielago
We start with the first grille. Create a SDS rectangle with dimensions U=4 and V=4. Rename the object to Grille_1.
SDS rectangle with U=4 and V=4 added
This grille is roughly shaped like a cube with tilted sides (well very roughly..). First move the edges that bend the grille. Because the blueprint lacks this level of detail, you need to closely observe the reference images and estimate the shape and position of the edges.
Move these edges
Then in Edit Points mode, move the points to match the shape as in the reference photo. Probably it will be helpful to switch to OGL (shaded) display for this. Then in Edit Edge mode select the top edge row and set Edge Sharpness to ‘Semi Sharp‘. When done, move the object in position.
Select the top edges and set them to Semi Sharp
Then we have a second Grille, just above the license plate area. This object is also created from a SDS rectangle. This time use U=2 and V=4. Rename the object to Grille_2.
Grille_2 starts as a simple 4 by 2 SDS rectangle
Then take a top view and align the Grille_2 object with the rear bumper area.
This object needs to be aligned to the rest of the rear section and you get this! (top view)
Next select the lower points and move them outwards (see reference image and next screenshots for the required position). Then also select the top left point (vertex) of the object and also move it in position:
Select these and move outwards to cover the indentation
Next, select top left vertex and move it!
Now switch to Edit Edge mode and select all edges, except the ones on the mirroring axis. Set Edge Sharpness to ‘Semi Sharp‘ and then extrude the selected edges just a little backwards (to the inside of the car).
Select these edges, set them Semi Sharp and extrude them
Make sure the mirroring axis is at X coordinate 0,00 and you’re done!
Three Grille’s ready!
Then it is time to model the taillights. We start with duplicating the Rear Bumper. Rename the duplicate to Taillight. You have seen the trick before: add faces by extruding them and modify the shape in Edit Points mode to match the blueprint.
Faces added to the duplicated object, points moved in position
With these faces still selected, invert the selection (press Ctrl + i key) and delete the faces you don’t need. Then for clarity change the color of the remaining faces (we chose red):
Remaining faces colored red
Make sure all points are in the right place. Then add in Edit Edge mode add faces, like shown in the next two screenshots:
You start like this…
and add faces like this!
Then, to finish it all off, switch to Edit Edge mode and select all outer edges and, like you did with the Grille’s, extrude them backwards (towards the inside of the car). Then set these for these edges the ‘Edge Sharpness‘ to ‘Sharp‘. And this concludes this chapter! :)
Edges selected, extruded and set to Sharp
Save your work now, before you continue!
All together now…
Time to finish the modeling process. Of course, many finer details can be added, and we leave that to your imagination and skills. As you know, the car is now half modeled and half mirrored, using an instance level. Let’s have a look at the merging process, so you are able to create a whole car from two halves.
Select the Lamborghini directory, and open properties at the Gen tab. Check if the directory is at X coordinate 0,00.
Select the Lamborghini directory and see if the translation X value is 0,00
With the use of the Instance, the objects with points at the mirroring axis where the modeled and instanced objects meet, are not automatically connected or merged. If left unfixed, this causes all kinds of minor irregularities and artifacts when rendering. This means we must manually mirror and connect all these specific parts. All otherparts, which are not at the mirroring axis, remain mirrored with the use of the already mirrored instance.
To distinguish objects that need manual mirroring from the mirrored instanced objects we create a new level directly under the Root level. Call it ‘Lamborghini-Murcielago’.
New level added
This new level will contain, besides the Lamborghini and the Instance level, all objects that need to be mirrored manually. Don’t worry, it’s not that many objects ;-)
Set the X coordinate for the level at X= 0,00. Drag and drop the following parts in this level:
Hood
Front Spoiler
Roof
Rear bumper
Side Rear
Windshield
Rear Window and Lamellae
Now we can merge the parts at the mirroring axis. Let’s start with the Hood. First thing we do is move the transformation handles exactly to the mirroring axis.
The hood with transformation handles roughly centered
Apply the Move command, with target set to ‘Handles’
And move the handles to the mirroring axis
Next we duplicate the Hood and apply the Transformation -> Mirror tool with the ‘About COG‘ option set.
Mirror tool selected and the ‘About COG’ option set
Next, multi select both objects (original Hood first) and apply the ‘MergeO’ (Merge Objects) tool. If you would render the Hood now, you would still see irregularities along the mirroring axis here and there.
The Hood duplicated and mirrored. The arrow points at the seam,
which is clearly visible.
The tool to use in situations like this is the JoinF (Join Faces) tool. We mentioned this tool before in this tutorial so you know how it works ;-). But, just to be sure, you need to set the Distance parameter and you must use a low value, like 1 or maybe even less.
The same Hood, after we applied the JoinF tool
Repeat these steps for all other objects along the mirroring axis of the car.
Now it becomes obvious why we asked you in the beginning of this tutorial (modeling the Hood) to set the vertices along the mirroring axis exactly at X coordinate value 0,00. You are about to join/merge several complex objects and you want the JoinF tool to only merge the vertices (points) along the mirroring axis. If you set a Distance value too large, also points farther away from the mirroring axis will also be merged. The results can be disastrous, to say the least.
This concludes this chapter, when you have done all the mirroring and merging don’t forget to save your project.
The textures of the beast…
This chapter contains some extra info about texturing the Lamborghini, Let’s start with the license plate:
License plate
The license plate needs a texture to be mapped on the license plate object.Here is an example of a texture file for the license plate:
License plate texture (gif format).
You can of course use your favorite paint program to create your own license plate texture. The one shown here is designed in Gimp, for a German car. Save this image if you like, so you can use it when creating your own license plate.
First we need to create a new VSL material. In the material tab of the Select window, press the right mouse button and select:
‘New -> VSL Material‘ from the pop-up menu. A new material will be added at the bottom of the list, rename that to
‘Licenseplate-Front‘
New VSL material selected
Then perform the following steps:
1. Select the Licenseplate-Front material and open the properties;
2. Check the Preview and the Advanced checkboxes (this gives you access to the VSL objects);
Preview and Advanced activated
Drag and drop a Shader object onto the Material icon. This adds a new object, called Surface Properties, to the VSL hierarchy. Then add a Texture object. Just drag and drop it on the Surface Properties object. In the lower part of the VSL Property Window (texture tab), you can select your texture file. Note that when you select the file, the preview sphere of the material is updated immediately.
Texture object and texture file added
Next, drag and drop a Constant object on the Surface Properties object. A new object is added, called ‘Color=Constant(0,0,0)’. Also note that the preview sphere at the top turns black. Then at the bottom of the window, you can change properties for the Constant object. Click the In/Out tab and select ‘Surface: Reflection‘ from the list. Note that the name of this object in the VSL hierarchy changes to ‘Reflection=Constant(0,0,0)‘
Drag and Drop a Constant…
Change Output to Surface: Reflection
Then, also at the bottom of the property window, click the Constant tab, and change the value to 0,18 0,18 0,18. Note the change in the VSL hierarchy and note the changed brightness of the reflections of the preview sphere.
Now add a new Shader to the VSL hierarchy. Just drag and drop it on the Material icon. Change the Shader Type to ‘Surface Illumination‘. Note that the name of the new object changes from Surface Properties, to Surface illumination. To finish the VSL material, drag and drop a Specular object on the Surface illumination object.
Set Shader Type to Surface illumination…
and drag and drop a Specular on the Surface illumination
The VSL material is now ready and you can close the VSL editor. To apply the material, simply drag and drop the material icon (from the Select window – Materials tab) on the License plate object. Realsoft3D will automatically use the proper mapping type for the object.
Texture applied. You’re done!
The tires
To texture the tires, we will use both bump and color mapping. Here is an example bump map texture for the tires. You can create your own, or use this one:
Texture used for bump mapping (gif format).
Create a new VSL material and call it Tire. Open the VSL property window, check the Preview and Advanced boxes. Drag and drop a Shader object on the Material icon in the VSL hierarchy. This creates a Surface properties shader. Add a texture object (drag and drop it on the Surface properties shader) and select the image you wish to use for the texture (in our case the Pirelli P3000 image). Then set the Bleed X and Bleed Y checkboxes. The Bleed option extrapolates texture edge colors outside texture mapped area:
Texture added, Bleed X and Bleed Y checked
Then drag and drop the Bump icon on the Surface properties shader. Click the General tab and set Operation to ‘+’ and now your VSL shader looks like this:
Bump map object added, Operation set to +
Then we use a simple parallel mapping to texture the tire.
Parallel mapping added
If you now would make test render, you will notice the dark and dull texture of the tire. This can be easily fixed, by adding a Constant object. Drag and drop a Constant on the Surface properties shader. At the bottom of the VSL editor there are three tabs. Click the Constant tab and set the Color value to 0,157 0,157 0,157 (a shade of grey). Click the General tab and set Operation to +. Note that the color of the preview sphere changes to light grey.
Note: If you have set the number of decimals to 2 (in the menu: Preferences -> Options -> Metrics tab) you will see that the value for Constant you just entered is truncated to (0,16 0,16 0,16). In the VSL hierarchy however you see three decimals (0,157).
Color constant added, Operation set to +
Then to add some shininess to our tires just add a Surface illumination shader, just like you did with the license plate. Then drag and drop a Specular object and set Sharpness to 2,10 and Brightness to 0,48. See next image:
Surface illumination shader and specular object added
The VSL material is now ready. Close the VSL editor and try your VSL shader! Here is a test render:
A test render of our textured wheels!
Painting your car…
Vesa Meskanen created two car paint shaders specially for this tutorial (thanks Vesa!). Applying the shaders is easy: just select a car part and drag and drop the shader and you’re ready. You can download the shaders by clicking here. Unzip the file and load the shader in the materials tab of the Select Window via the Right Mouse pop-up menu (‘Paste from a File‘). This adds two new shaders at the bottom of the materials list, called carpaint and metal_paint. Also it adds a sky, which can be used with a self illuminating dome over the scene.
Insert a shader from file..
Simple tests showing the two shaders
Of course you can change the appearance of these shaders if you like. For instance, select the carpaint shader in the Materials tab of the Select Window and open its Property Window. Make sure you have the Preview option set, so you can see the effect of your changes immediately. By default the shader allows you to change the base color, specular color, specular sharpness and specular brightness. Changing the base color changes the color of the carparts with this shader. The specular color defines the color of the highlights. If you know your way around in VSL, set the Advanced option to access the VSL statements and have even more control over these shaders. Just play around with the settings and see what results you like best!
User interface of the carpaint shader.. and the more complex metal_paint shader.
The Grille’s
The Grille’s basically are black plates with lots of holes in them. You could decide to manually cut out these holes with the Boolean Remove, or you could use a clipmap for this purpose. Considering the number of holes you need to make it look good, we suggest you use the clipmap technique. With a clipmap it is possible to define a color range, which removes the underlying surface. You can use this small texture file as the clipmap texture. (kindly created and donated by Bernie den Hertog).
Let’s see how this works. At the materials tab of the Select window, right click and select New -> VSL Material. Rename the new material to ‘Grillestexture‘. Open the Property window for the Grillestexture material. Enable the material preview, so you can see the effect of your modifications. Use the Wizard to add a Clipmap. Then in the FileName field select the Grillestexture.bmp file.
Clipmap selected in the Wizard…
texture file selected which will act as a clipping texture
This material may look complicated at first, but it’s not that bad. The following controls are used in the clipmap material:
Filename: the name of the texture file used for clipmapping;
Sub channel 1 min & max: These two values define the clipped red signal range;
Sub channel 2 min & max: These two values define the clipped green signal range;
Sub channel 3 min & max: These two values define the clipped blue signal range.
You need to define a color that you wish to cause the clipping effect. If you click the Show button, the selected texture is shown. In this case it is a dark grid like texture, with dark grey holes in it. The holes will be used as ‘cutters’. With the Sub channel controls you need to find the combination of values that cause a clipping effect. The good thing about grey is that the RGB values are the same, so the sub channel values must also be the same for each of the three sub channels. Take a look at the next image to see the correct settings:
Setting all sub channels at the right value causes a clipping effect!
Enter these values as shown above in the material Property window and then close it; the material is ready. The grille is not a very large object and you need small holes. Select a grille object and apply the Grillestexture as a parallel mapping and make the texture object square shaped. Use small dimensions: the larger the texture object, the bigger the holes! The last step is to set the color of the grille object to a very dark grey (0,16 0,16 0,16) via the Properties -> Col tab.
One of the grille’s. The white square is the applied clipmap. A rendered close up of the applied clipmap against a blue self illuminating background
You can of course apply the same material to the other grille. Save your work before you continue!
Rendering the Scene
This is the final chapter of this tutorial and it will explain how to set up the scene for rendering the image you have seen at the very beginning of the tutorial.
Setting up the environment
Your car is now ready and needs an environment. We keep it simple here. Take a top view and add an Analytic rectangle. This will be the floor the car stands on, so call it Floor. You can texture that if you like and it is a good idea to make the rectangle infinitely big. To do that: select the rectangle, open Property Window at the Spec tab and check the Infinite checkbox.
Realistically rendering objects with shiny surfaces, like this car, requires the use of GI (Global Illumination). Setting up the environment for GI is easy. Create a new level under the Root level and rename that to GI Scene. In that level create a new level via the Layers -> Environments -> Sky menu. This adds a new level object to the hierarchy, called Environments. This contains a wireframe invisible mesh in the shape of a dome (or hemisphere). To carefully position the dome, make the mesh visible again by unsetting the WF Inv in the MiscTools toolbar. When done, make it WF Inv again.
Adding a sky dome to the scene
Then drop the Floor, the Environments and the Lamborghini into the GI Scene level. Select the GI Scene level and add a GI shader to it. Finally, under the Root, add a camera object. The hierarchy looks like this now:
The hierarchy after GI setup
Basically the setup is done, now it’s time to do some tweaking and customizing. Let’s start with the Environments level (our sky dome). Select the mesh level inside the Environments level and open its properties at the Col tab. Make sure the texture map method is set to Illumination map and select your favorite sky texture. Illumination maps add diffuse light (no hard shadows) to the scene using the colors of your texture. So if you take a blue sky, the effect is that bluish light is added to the scene; change it to a darker, orange yellowish sky with a sunset, and the effect on your render changes dramatically. It is advisable to set up some simple scenes (just a shiny sphere on a floor) and test (small 200 * 200 renders) the outcome before final rendering.
Properties for the sky dome mesh
Global illumination
Next, let’s have a look at the GI. If you would now render the scene, the resulting image probably will be quite dark. Note that you don’t have any light sources in the scene (maybe except the standard flash light settings in the camera object). You can add light sources if you like, but it is not required to light the scene in this case.
The GI rendering results are a combination of several ingredients:
1. Brightness of the colors used in the sky dome texture;
2. Settings in the current scene camera
3. Settings in the GI_shader you applied to the scene;
4. Settings in the Post Image Effects tab;
5. Settings in the File Rendering window.
Camera
The colors in the sky dome already have been addressed here, so let’s have a look at the camera. Select the camera object in the hierarchy and open its properties at the Spec tab. For the best results, when working with GI, it’s advised to set the Flashlight to black. Click the grey colored icon and select a black icon in the colors window that pops up. You can also manually enter three zeroes (with spaces in between) at the input field; the result is the same:
Flashlight set to black for better GI results
GI_shader settings
The manual explains rather in depth how the GI_shader works (have a look at the Advanced Illumination Examples, specifically at the Global Illumination Components paragraph). An excerpt from the manual, about the controls of the GI_shader:
RayCount1 – The amount of GI samples at surfaces directly visible from thecamera. Usually this is the most important quality setting for indirect illumination. The higher the sampling, the lower ‘Iterations’ value can be used in the ‘GI_blur’ filter. The result is finer detail and higher realism in global illumination.
RayCount2 – The amount of GI samples at reflected surfaces. Increasing this helps to render sharp, noiseless mirror reflections of indirectly illuminated areas of the scene.
RayCount>=3 – The sampling quality for surfaces visible through double reflections, glass etc. Increasing this value helps to render sharp, noiseless images of indirectly illuminated areas of the scene which are visible through glass objects.
Contrast – Enhances local details in the global illumination. Weakly visible surface details such as low bump maps tend to disappear in strong indirect illumination. Increasing Contrast makes them more visible.
GI Bounces – The tracing depth of indirect illumination. Usually 3 bounces is enough. However, in special situations, such as when the indirect illumination comes through glass layers (windows), higher values may be necessary. Higher values also increase realism and brighten the image.
GI Reflection – Controls the brightness of indirect illumination that is visible through reflections and transparent objects
Basically it comes down to the following rule: higher ray counts produce better images (less grain), but you pay for that in terms of rendering time. You have to experiment for your own and that takes time. Try values like 10 or 15 for Raycaount1 for starters. Use small image sizes (like 300 * 200) when doing tests saves a lot of time! Also when testing, in the File Rendering window, make use of the Render and Backup Ray Trace option and Post Process option.
Real time savers, these options in the File Rendering window!
Post Processing
Using GI also requires you make use of the post processing system that Realsoft3D offers you. In the Select Window, click the Post Image Effects tab. Then double click on the GI_effects icon. The GI_effects basically is a container with some effects inside. You can add or remove these ‘inner effects’ simply via the properties of the GI_effects. To apply this ‘container of GI_effects’ to your scene you have to drag and drop the GI_effects icon from the Post Image Effects tab in the view window. After modifying one or more effects inside the GI_effects container, you have to drag and drop the GI_effects icon in the view window again to make your changes effective.
Double click on the GI_effects icon and you get the following window:
The GI_effects property window
The lower half of the window shows the list of effects that are ‘ inside the container’ and there are some in the list you don’t need. Select the Render particle effects and then click the Remove button. Repeat that for the Render glow material properties. For each of the effects in the container, you can change the properties as well. This is done in the Post Image Effects tab itself. There are two important effects in the container we wish to address here: GI_brightness_control and GI_blur.
As the name already suggests, GI_brightness_control gives you control over the overall image brightness. The brightness is controlled via a curve. You can access the curve by double clicking on the GI_brightness_control icon in the Post Image Effects tab. The curve shows the RGB values of the knot points on the curve. You see only the red curve, because it is exactly on top of the blue and the green one. So it is possible to change, for instance, only the red component in the image to brighter or darker. If you click and move a knot point, the underlying curve appears. To select all curves at the same time, simply drag a box around the knot point and then move it. Which curve shape is best, is again a matter of trying out. Keep the curve’s minimum and maximum values between 0 and 1.
This curve produces rather dark results…
and this curve produces much brighter results!
The GI_blur is a time consuming parameter: higher values lead to longer render times. GI_blur blurs out the grain which is caused by low ray counts in the GI_shader. Remember that heavy blurring can cause loss of detail and also leads to longer render times. Try for instance Blur level = 7 and Iterations = 10 to start with. Again, you can decide the parameters here, testing will tell you which settings are best.
Blur Level = 7 and Iterations = 10
File Rendering Window
The last part in the setup is the File Rendering Window. As you probably know, this window has a lot of options. Here we only want to make sure that all the settings you have applied in your scene are also taken into account when rendering the image. The important part here is the Settings section. You must have selected GI Rendering in the Rendering Settings field and GI_effects in the Effect/Image field. If you forget this, the image will render with the default rendering configuration and there will be no GI applied.
Rendering Settings and Effect/Image are set for GI
This concludes our tutorial. Thanks for taking the time to read it and try it all. Share your results on the mailing list! And if we can do anything to help, just let us know.
Robert den Broeder (aka ‘Spliney’)
Stefan Klein (aka ‘Blockbuster’)
July 2006.