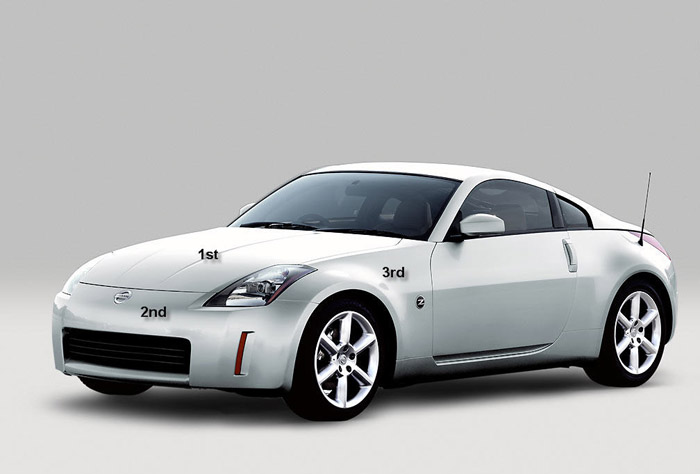
How to create a model of a sport car – Nissan 350-Z
This is a step-by-steptutorial that explanehow to create 350Z’s body using polygonal modeling in Maya environment,but you can apply this technique to other poly-modeling software.
Step 1
This is my screen-shot after I have correctly placed my blueprints.
Step 2
To start with, we’ll concentrate on the front part of the car. I’ve divided it into 3 parts just like it is in real life too, each part is defined by cuts as shown in the picture. Start with the modelling of part 1. Car Detailing Introduction – Many people mistake car washing with car detailing. Looking for Car Detailing? Provides an overview of car detailing and how it’s different that a simple car wash or wax job.
Step 3
Create a polygonal cube () and using the Scale and Move tools try to give an approximate size of the part of the car that we want to model like top10slotgames casino cruise review. You should have something like this.
Step 4
For a better control over each point of the surface, we must subdivide our cube in more sections. To do that, select the cube and go to the Channel Box (, on high on the right). Roll down until you see the PolyCube1 point, this is the name of the cube that we have just create. Do double click on the name, to open the Property of the object and set the Subdivision With to 6 and the Subdivided Depth to 2. Now, do one click on the write PolyCube1 and change the name if you want. Move to the Side View and eliminate the faces behind and below. Make the same for the faces of the superior half in the Top View.
Step 5
Now, selecting and moving the vertexes, try to give it a more defined form as possible, following the blueprints in all the three view. The result should be like in the screen-shot.
Besides I’ve eliminated the lateral faces that don’t serve me.
Step 6
For define our model, we have need of other polygons (subdivisions). To do this activate the Split Polygon Tool command () and in the Top View, traced some lines (the lines must start from one edge and finish on another one, and at the end you must confirm that with the Enter button on your keyboard) in the parts that request a major control, and adapt the new vertex to the blueprints. Try to not abuse of the Split Polygon Tool command, this is important, try to create only polygons that serve you. More useless faces, become only a problem because the surface become then uncontrolled.
Step 7
To make a cut on the hood begin to define the form using the Split Polygon Tool. Unfortunately the cut that we want to do, don’t coincide with the end of the piece that we modeling in none of the two extremities, that will tends to create some difficult and problems. Remember that the polygonal models in Maya must have 4 edge (namely 4 vertex), so try to avoid polygons that have 3, 5 or more edge because them tends to create problems with the smooth comand.
Step 8
In the last screen-shot you can notice that we have create 3 irregular polygons that must be adjust: from 3, 5 to 6 edge/vertex. Using Split Polygon Tool try to build 2 lines like in the picture.
Step 9
And after this, delete the 2 edge like in the picture.
Step 10
In this mode, where there was a triangle, we have create a polygon composed by 4 vertex.
Step 11
Adjust also the position of some vertex making the surface more ordered.
Step 12
Delete the irregular faces by tracing with Split Polygon Tool a few lines this way (in tool options () turn off Snap To Edge and Snap To Magnets), in fact as you can see now all faces are done by 4 sides.
Step 13
Adjust the position of some vertices with the Move tool. I advise you to assign to the bonnet some reflective shader like Phong of a not too dark color, in this way when you do the Smooth you can notice better possible present faults on the surface.
Step 14
Now we pass to the other end of the cut that demands a similar procedure. A very important note: try to follow the direction of the surface that been modeling, otherwise the result will be worse. As an example, see the screen-shot next, with the arrow I have tried to evidence the direction of our cut. It is very important to be able to see the right direction of surface because is that that at the end determines the “professionality” of your job.
Step 15
Let’s begin with tracing a line that delimits our cut and of continuation also two lines parallels like shown in the screen-shot.
Step 16
With Split Poligon Tool you divide our polygons in this way.
Step 17
Now select edges that are of devious to our curve and delete them (not forgot to delete the vertices that remain after you’ve eliminated edges).
Step 18
If you have noticed, now the direction of faces follows our curve perfectly.
Step 19
Finally we trace a pair of lines in this way in order to eliminate two polygons by 5 and 6 faces that we had before and consequently we fix the position of some vertices trying to align them to the blueprints.
Step 20
At this point the bonnet nearly is near to be complete, only lacks the “control lines” to its edges (not on that inside) that they serve in order to better define its shape during the Smooth. You also I have shown one of the ways in order to eliminate the triangle that is come to form in proximity of the beacons.
Step 21
We work newly with Split Polygon Tool in order to divide the polygon from 5 sides in two from 4. Controlled moreover for the last time that all you concern are perfectly aligns to you with the blueprints. You can apply Smooth Linear with set up level of subdivision to 2 in order to see as the cowling is coming discovering even eventual defects to correct.
Step 22
Moving some you vertices I have created the part of headlight. After with Split Polygon Tool I have added some line in order to better define the obtained result.
Step 23
At this point the bonnet can be considered (nearly) finish. It lacks, in fact, still the depth sense (thickness) but we will think about it at the end when we will have completed the body of the auto. Create a new level, name it in way as better you believe and assign to it our job, so you can hide/show it in every moment.
Step 24
If you want to see as your cowling is coming, it selects it and dates to you the Mirror commando () and therefore also the commando Merge Vertices with the formulations of default, and finally a beautiful Smooth Linear with level of subdivision set up to 2. This is the result that I have obtained.
Step 25
We begin therefore the modeling of that we have indicated initially as it leave Analogous n.2. to how much we have made before, we leave constructing a poligonale cube and we try to adapt it to the approximate shape following the blueprints.
Step 26
Enter in Channel Box and under PolyCube1 set up Subdivisions Width to 6 and Subdivions Depth to 3, also change the name of PolyCube1 in something user-friendly of your choice. Delete back and below faces and also superior half in Top view.
Step 27
Try to give a more consistent shape moving vertices in the 3 views and eliminating a pair of faces.
Step 28
With Split Polygon Tool I have fixed the situation in right angle at the top and I have aligned vertices to blueprints.
Step 29
We begin to define the part of the headlight by tracing a line and eliminating the two faces that are in place of the headlight.
Step 30
In this screen-shot I have evidenced the direction of the surface and therefore the direction that must assume the faces/edges in that zone.
Step 31
Trace one line in this way under the headlight.
Step 32
Move these three vertices in depth aligning them with the blueprints.
Step 33
In this screen-shot I’ve shown little simple passages with which I have eliminated some problems. As far as the two union vertices concerned, not forgot to activate Snap to Points () that it will allow you to more close couple the apex during the movement. After to have them united not forgot to select them and do Merge Vertices (
) in order to merge them, that is to create an only one vertex (even if were found in the same point, were however two you concern separates to us to you).
Step 34
Trace another 3 lines in order define better that zone after the Smooth.
Step 35
As you can see, now the part of headlight has the direction that we wanted to.
Step 36
Traced an other line and having more control in this way aligne the new vertices to the blueprints.
Step 37
Use Split Polygon Tool newly for traced the following lines.
Step 38
Moved new vertices in depth and eliminate some problems with the irregular face in the ways indicated in this screen-shot.
Step 39
Before continuing we newly observe the direction of the surface in this part.
Step 40
Define the arc over the wheel creating new lines and moving them in intentional position.
Step 41
Trace this lines.
Step 42
For give the demanded direction to our surface we must delete some edges and consequently also vertices that they leave.
Step 43
Now move newly vertices and align them with blueprints (I advise you to see). As far as the triangle that has been formed in bottom, the solution is much simple one. With Split Polygon Tool fairies click on the external side of the triangle and dates Shipment. In this way you an apex has been created, that it means that hour that polygon has 4 concerns to us and therefore 4 sides.
Step 44
Trace another two lines in this way in order to define better the angle low to right during the Smooth. Notice moreover the direction of the faces that we have obtained.
Step 45
By adding, removing and moving vertices try give it a nearly definitive shape.
Step 46
To this point in order to end the piece it lacks to only model the hole to us. In the several sights tried to define the shape of the hole moving you concern and adding new sides to us with Split Polygon Tool.
Step 47
Before proceeding with next passage control that in the menu Polygons Tool Options the voice Keep Faces Together is active. Selecte the faces of the hole like indicated in the previous screen-shot and use Extrude Face (). The so-called Manipulator Tool with 4 arrows appears: 3 of their (red, green, blue) are need to control the direction in which the command must be applied, while 4° (with blue button to shape of circle in top) is need in order to change the plane of reference regarding which the 3 arrows move before. This last one can be of 2 types: universal and local. The first one, universal, is independent from the object on which you are working and can be represented by the grid of the scene. That local one instead, refers to the plan of the object, in the sense that the transformations happen in the direction of the plan just of the object (or the single faces or sides) on which we are working. Try to change Manipulator Tool from premises (on which it is set up initially) to that universal one in order to understand the difference better. As far as our hole, after to have selected the faces and activated Extrude Face, changed the Manipulator Tool to that universal one and moved leggermente one of the arrows in the demanded direction. You press Extrude Face newly, changed the manipulating newly and moved the arrow before in the same direction but a po’ more far away. Finchè is still active the manipulating presses Delete on the keyboard in order to cancel the faces, since more does not serve us. The obtained result would have to be similar to this.
Step 48
Eliminating, moving and adding new lines they have arrived to this result.
Step 49
Finally, aligned the position of you concern us of the hole created with the blueprints and traced other lines in order to define that part better.
Step 50
To this point the modeling of our bumper can be considered concluded. Created a new level with a name to chosen and it assigns them our model to you. This is the result that I have obtained.
Step 51
In order to end the facade of our machine lacks us last part. We begin as usual with the construction of a cube.
Step 52
Set up Subdivisions Width to 2, Subdivisions Height to 4, Subdivisions Depth to 5 and cancelled the faces of under, of behind, of and those inner ones.
Step 53
We eliminate moreover these polygons in order to succeed to model the arc over the wheel.
Step 54
Now move the single vertices trying to give an adapted shape.
Step 55
Trace the this line following the arc of the wheel and delete triangle with the indicated method (outlined line is the situation before, while that red one is like would have to be).
Step 56
I have aligned newly you concern to us and eliminated an other triangle.
Step 57
We begin to in this way give to shape to the zone of the beacons eliminating a pair of faces and adding one line.
Step 58
This passage is similar to the previous one.
Step 59
Eliminate following edges with the vertices that they leave.
Step 60
Traced therefore these lines following the direction of the arc.
Step 61
We eliminate the irregular faces.
Step 62
I have eliminated a line that did not serve to me and with a little patience I have aligned newly you concern to us.
Step 63
I have added some line of control in order to better define the surface in the important zones.
Step 64
Others two lines.
Step 65
I havedefined better the part of the beacons having traced new lines and eliminating the others.
Step 66
To this point the frontal part of the machine can be considered concluded. Tried to make the Smooth with the same formulations that you have used before, if there is something that does not convince tried to fix it to you with the instruments used in the previous passages.
Step 67
The next element of our modellazione will be nothing less than the door. Created a cube, adapted its dimensions to the blueprints, settate Subdivisions 4 Height to and Subdivions Depth to 3. Eliminated the faces of behind, of, of over, of under and those inner ones; in this way you it remains only a flat object with which we will work.
Step 68
I have aligned the several one you concern to us with the blueprints and therefore I have added to others two lines in order to define the surface better.
Step 69
With Split Polygon Tool I have always added of the control lines in order to better define the edges of the door.
Step 70
And in order to end, a pair of lines in order to render the angle of low possible the acute fold.
Step 71
To this point you take the part that we have modeled before and tried to align them one with the other. In the case in which there was need you can trace some extra line like I have made I.
Step 72
This is the result that I have obtained applying the Smooth.
Step 73
The piece under the door for hour the lasciamo to be, we begin instead the modellazione of the posterior lateral part beside the door. Created a new poligonale cube, it moves it to you from the part of the element that we want to model, adapts it to you to the measures and set up Subdivisions 4 Height to and Subdivisions Depth to 4. The faces except those external eliminated all analogous to as we have made with the door.
Step 74
We eliminate other faces.
Step 75
Now moving the single ones you concern we try to give a more credible shape to us.
Step 76
With Split Polygon Tool we try to define the arc better.
Step 77
We put in order our surface eliminating the triangles and aligning you concern to us. Tried moreover to give an approximate shape in the 3 dimensions.
Step 78
Tracing some lines I have defined the arc better.
Step 79
To this point I become account that the position data offers from blueprints me are not more sufficient and therefore active the sight gives behind the place of that facade.
Step 80
Having new blueprints we align newly you concern to us and therefore we trace some line in order to define the arc.
Step 81
Last modifications in order to end the job on this piece.
Step 82
This is the result that I have obtained applying the Smooth.
Step 83
We begin to put some mattoncino for the lateral part low, that one that finds under the door (served us the piece who we have hardly made). Created a cube, adapted its measures to the blueprints, set up Subdivisions 2 Height to and Subdivions Depth to 7. The faces eliminated all fuorché those external analogous to as we have made for the door. In the Side sight I have moreover moved some you concern us from their position originates them in order to adapt the surface to the successive modifications.
Step 84
Eliminate the 3 faces in means and tried of dargli an adequate shape.
Step 85
Work a little with Split Polygon Tool.
Step 86
Also this piece can be considered ended. Fixed the position of the several one you concern to us if you have not still made it and tried to make the Smooth. This is the result that I have obtained.
Step 87
We begin therefore the posterior part of the machine. As usual we create a new cube, we adapt it to the measures of the piece that we want to model and we set up Subdivisions Width to 8, Subdivisions 3 Height to and Subdivisions Depth to 2.
Step 88
In the Top sight we eliminate the advanced half of the faces, while in the Side sight the faces low, up and those inner ones.
Step 89
We begin to dargli an approximate shape moving you concern to us. We eliminate moreover some faces that do not serve to us.
Step 90
I am tracing some line in order to define the arc and one line in order to define the part of the beacons. With Split Polygon Tool I have always created an apex on the external part of the triangle that has been formed and I have moved it like in the image.
Step 91
I have defined the angles better.
Step 92
Tracing of the lines and eliminating the others, I have delimited the cavity that contains the plate.
Step 93
Selected these faces and with Extrude Face tried of dargli the intentional forma/profondità.
Step 94
Eliminated the lateral faces of the object as soon as extruded (those that are coincided when Mirror is executed) and aligned you in this way concern us to the main axis of the grid (used Snap to Grid ().
Step 95
Hour we see to make the hole of the beacons that is found next. We trace one line in order to delimit our hole in this way.
Step 96
Between an adjustment and the other has arrived to this situation.
Step 97
In order to end, fairies a double Extrude Face: one to small distance regarding the point of departure, and the other a po’ more far away. Eliminated the faces in bottom.
Step 98
I have circumscribed the hole with a pair of lines in order to define it better.
Step 99
Same thing as far as the cavity of the plate.
Step 100
To this point fixed the surface, if ce of need, in such way to render more it smooths down it and it continues possible.
Step 101
Hour all the sides of the line selected low.
Step 102
Used the commando Extrude Edge () (the operation is identical to Extrude Face, solo that instead that with the faces he works with sides) in order to obtain a similar result (some you concern to us I have moves them manually to you).
Step 103
The modellazione of this part is concluded. Rechecked in order your surface and fixes it well to you if ce of need. This is my result.
Step 104
We begin the modellazione of the part that finds over the piece that we have hardly made. Created a cube, it adapts it to you to the approximate measures, set up Subdivisions Width to 8, Subdivisions Height to 2, Subdivisione Depth to 3 and eliminated as usual the faces that do not serve to us.
Step 105
We begin to dargli one sure shape.
Step 106
We eliminate some faces.
Step 107
To this point diamogli a preciser shape.
Step 108
I have added to some line of control in the critical points us.
Step 109
This is the result that I have obtained.
Step 110
Hour us lacks only a piece to model in order to end the auto body, the roof. Created the cube, it adapts it to you to the measures of the roof, set up Subdivisions Width to 6, Subdivisions Height to 3, Subdivisions Depth to 3 and eliminated the faces that do not serve to us.
Step 111
Eliminating some faces and moving you more concern diamogli an adapted shape to us.
Step 112
I have added some line in order to define some points better.
Step 113
Hour, siccome the roof of the machine is constituted from two pieces (the roof and the supports) we will make it equally. Selected the faces of the roof and cliccate on the Extract commando (). Hour the roof is divided in two parts.
Step 114
Like last phase of the modellazione, I have added of the lines of control to the edges of both models.
Step 115
This is the result that I have obtained making the smooth.
Step 116
To this point the modellazione of the auto body substantially is concluded. Tried to render all the levels visible in order to see the machine in its together. It would have to be something of similar.
Step 117
Hour we will try to give a little “depth” to our auto body. We as an example take to the frontal part of the machine (that composed from the cowling and bumper) and select these sides.
Step 118
Cliccate on the commando Extrude Edge (that we have already used for the posterior part of the car), changed the manipulating to that universal one (of hour and in ahead used only this, that premises it is not adapted for our scope) cliccando in top to 4° the arrow and leggermente moves it to you to the inside. Cliccate newly Extrude Edge and moved the manipulating in the same direction but this time more far away. Similar what would have to come you outside one.
Step 119
In order to see com’ it has come tried and to specchiare is the cowling that the bumper (every time that specchiate an object not forgotten to give the commando Merge Vertices with formulations of default) and fairies the Smooth. This is the result.
Step 120
The procedure is much simple one, reason for which I am not to explain every passage to you but I will limit myself to illustrate some is made to you.
Step 121
This is the final result.
Step 122
We begin the modellazione of the glasses, more just those facades. Created a cube and in the Side sight the faces except one eliminated all in this way.
Step 123
Per.primo.cosa adapted the measures of the polygon to those of the E glass therefore with a subdivision (Split Polygon Tool) tried of dargli an intentional shape.
Step 124
This is my result.
Step 125
Same identical procedure for the posterior glass.
Step 126
The procedure does not change not even as far as the lateral glasses, than obviously they go models in two pieces separates to you to you.
Step 127
We try to render our glasses lateral more details adding the edges to you. We begin from that one centers them. With Split Polygon Tool traced the shape and therefore selected the faces.
Step 128
With Extrude Face (used the universal manipulating, not local) fairies 2-3 extrusions moving every turns the new faces towards the outside.
Step 129
The same procedure applies it to you also to the other edges. This has turned out that I have obtained.
Step 130
In the same way I have made also the beacons frontal.
Step 131
And those posterior ones.
Some particular like the small mirrors, the handles, tail pipes lack still, antenna etc, but task arrives you to this point that any of you that it has followed the tutorial is in a position to making them without large difficulties independently.