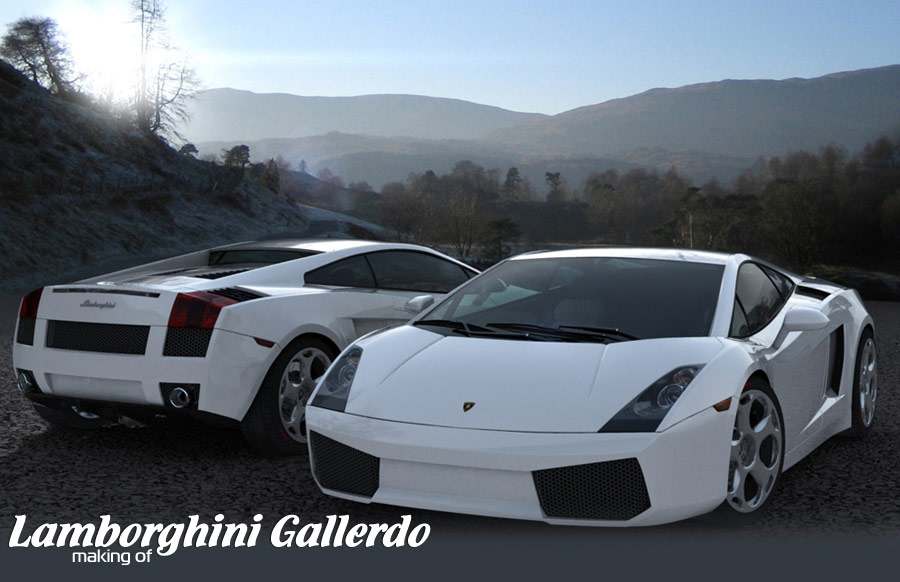
The Making of Lamborghini Gallerdo
This image was created for a personal project to brush up on my high-end skills, having only been working on lower poly game art for the past few years. The mesh is approximately 1.5 million polygons and Brazil r/s was used to render out the model.
![]() |
||
March 22, 2006 | Stryker
The beginning This is were this project began using top, side and front profiles mapped onto a box, the box has had its normals flipped and unused faces removed. One of the most important things when setting up your guide is to ensure that your blue print images have equal widths and height, and the box you use to map them onto is at the same proportion to the blue print images. If you get this wrong your car will be out of proportion!! You must also be aware that most blue print data isn’t 100% correct and should be used as a starting point for your work.
The second image shows a small increment of the construction using the extrude edge function, more geometry is created around the door and wheel arch area. In the second image the geometry around the rear wheel arch is being cleaned up before the separate wheel arch geometry profile is added to the main body shape. (black arches) |
||
![]() |

![]() |
||
Using instanced arrays
This is the final stage of the wheel array creation. The example object used to demonstrate the array is actually complete and the instanced array technique was used to get the shape and the form of the alloy wheels correct. Once happy with the shape and form of the wheel its time to break the instancing and attach the segments of the wheel together, the final stage is welding or stitching the vertices together to form the complete wheel. This can take time but thinking about how you can reduce and re array the segments will reduce the number of vertices you will need to weld together. The finished wheel and its components. |
||
![]() |

![]() |
||
Building in detail Below is the the rendered version of the tail light in a scene the grill effect is created using a bump map similar to the grill below in the bump slot and a coulred version in the glass filter colour (brazil r/s) The headlights |
||
![]() |
![]() |
||
Paintwork Fresnel Disk Brakes
The disk textures
3DM models creation |
||
![]() |